ZEON CORPORATION is a petrochemical manufacturer that maintains numerous products with a large share of the global markets including synthetic rubber used in automobile parts and tires, synthetic latex used in surgery-use gloves, and other products. The Company's strengths include its creative technology development function, R&D structure, and high earnings generation capability. Many of the products and materials manufactured by Zeon are used in a wide variety of products including automobile parts and tires, rubber gloves, disposable diapers, cell phones, LCD televisions, perfumes and other products commonly used in everyday life. The Zeon Group is comprised of the parent company, 58 subsidiaries and 9 affiliated companies. Zeon also has manufacturing and marketing facilities in 16 countries around the world.
(Company Name and Management Vision)
The company name "Zeon" is derived from the Greek word for earth "geo" (phonetically pronounced "zeo" in Japanese) and the English word reflecting eternity "eon," and reflects the Company's principle of
"deriving raw materials from the earth and perpetually contributing to human prosperity" through the development and application of creative technologies. (Zeon's original name "Geon," used at the time of its establishment, was derived from the trademark acquired for the vinyl chloride resin "Geon" from the Goodrich Corporation (then called B.F. Goodrich Company) in the United States, with which it had capital and collaborative technological agreements. The company name was changed to "Zeon" when the capital agreement was dissolved in 1970.)
(Corporate History)
Zeon was established as a joint venture company formed by the Furukawa Group of companies: Nippon Light Metal Co., Ltd., Furukawa Electric Co., Ltd., and Yokohama Rubber Co., Ltd. in April 1950 to acquire and use the vinyl chloride resin technology from B.F. Goodrich Chemicals Co.
In 1951, Goodrich acquired 35% of the shares of Zeon for full-scale technological and capital partnership, and in 1952 mass production of vinyl chloride resin began in Japan for the first time.
In 1959, Goodrich transferred synthetic rubber manufacturing technologies to Zeon, which, in turn, started Japan's first mass production of synthetic rubber. Manufacturing facilities were also expanded to match the growing demand for tires and other automobile parts.
In 1965, use of the Company's unique technology called Geon Process of Butadiene (GPB) for the efficient manufacture of butadiene (main raw material of synthetic rubber) from C4 fraction was operational.
Goodrich transferred its specialty synthetic rubber business to Zeon along with the shift in its main business focus toward vinyl chloride resins. Capital ties were dissolved in 1970. Along with these changes, the Company name was changed from Geon to Zeon in 1971.
Also in 1971, Zeon developed a unique technology called Geon Process of Isoprene (GPI) and began using it to manufacture raw materials including high-purity isoprene, hydrocarbon resins, and synthetic perfume ingredients from C5 fraction.
After entering the 1980s, Zeon aggressively launched new businesses in various fields including photoresists and other information materials, and medical-related applications in addition to its main synthetic rubber business.
In 1984, production of hydrogenated nitrile rubber Zetpol®, which currently has top share of the worldwide market, began at the Takaoka Plant.
In 1990, manufacture of synthetic cyclo-olefin polymer resin (COP) ZEONEX®, which is the main product of the specialty material business using the GPI method to extract and synthesize products, was started at the Mizushima Plant.
In 1993, Zeon entered China with its electronics materials business.
In 1999, Zeon Chemicals L.P. (Consolidated subsidiary in the United States) acquired the specialty rubber business of Goodyear Tire & Rubber Company of the United States to become the world's top manufacturer of specialty rubber.
In 2000, Zeon discontinued production of vinyl chloride resins at the Mizushima Plant, and thus withdrew from the Company's founding business.
Since the 21st century came, the company has been operating business actively, for example, by releasing ZeonorFilm®, an optical film for LCD, strengthening global production and sales systems, starting the commercial operation of styrene-butadiene rubber (S-SBR) in Singapore, upgrading the equipment for optical films for LCD in Himi-shi, Toyama Prefecture, starting the operation of the world's first mass-production factory for super-growth carbon nanotubes, and establishing a joint venture for manufacturing and selling S-SBR in cooperation with Sumitomo Chemical in Singapore.
(Business Description)
Zeon's main products use various extracted from naphtha, which is extracted by distillation of crude oil.
Zeon uses butadiene extracted in the GPB method developed in-house from C4 fraction after extracting propylene (C3), isoprene monomer (IPM) extracted from C5 fraction using the GPI method, high-boil monomer (HB), dicyclopentadiene (DCPD), and 2-butyne as raw materials to be processed into synthetic rubber, synthetic latex and various other materials.
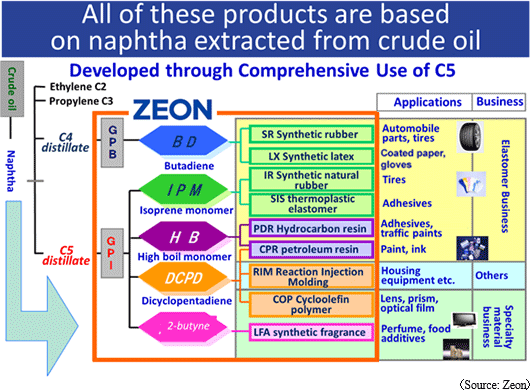
Zeon has three business segments: 1) the
elastomer business, where manufactured basic materials are sold to customers; 2) the
specialty material business, where basic materials are submitted to primary processing for sale to customers as processed materials, and 3) the
other business.
<Elastomer Business>
Elastomers are "high molecular compounds that have rubber-like elastic properties," an example of which is synthetic rubber. As described in the corporate history section of this report, in 1959 Zeon became the first company in Japan to mass-produce synthetic rubber, which became the foundation underlying all of Zeon's businesses. This business includes the segments of synthetic rubber, synthetic latex, and chemical products (hydrocarbon resins, thermoplastic resins) businesses.
① Synthetic Rubber Business
<Example of final product: Tires>
Zeon provides the world's leading tire manufacturers with the world's highest-quality synthetic rubber for use in tires. Among the various types of synthetic rubber manufactured are styrene butadiene rubber (SBR), which promotes superior abrasion resistance, aging resistance and mechanical strength properties, butadiene rubber (BR), which includes a superior balance between elasticity, wear and low-temperature properties, and isoprene rubber (IR), which features similar high levels of quality, consistency and other properties as natural rubber.
Zeon expects the demand for S-SBR for low fuel consumption tires, which further improved the characteristics of SBR, to expand rapidly in the future. In order to increase the supply capacity corresponding to this, Singapore plant started operation in September 2013 (the first line). The second line started operation in April 2016. The supply capacity of the Singapore plant is 70,000 tons.
<Example of product: Automobile Parts>
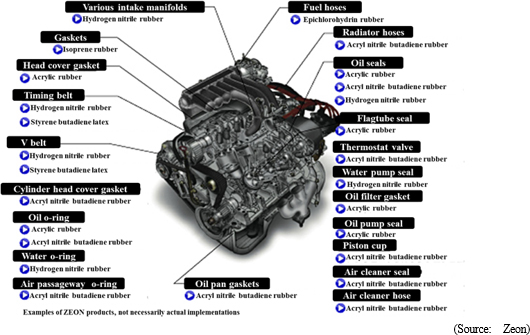
Radiator hoses, fuel hoses, fan belts, oil seals, and various other car engine parts use specialty synthetic rubber that has superior oil resistance and heat deterioration-resistant qualities. Zeon is the world's number one manufacturer of specialty synthetic rubber and features high quality levels and high market share of specialty synthetic rubber automobile parts. In particular, Zeon's Zetpol® hydrogenated nitrile rubber timing belts display superior heat and oil resistance and claims approximately 70% share of the worldwide fan belts market.
Furthermore, a new grade of Zetpol® has vastly improved the performance of products using the original versions of Zetpol®.
Products using the new grade of Zetpol® are heat resistant at temperatures that exceed the limits for the original version of Zetpol® by 15 degrees centigrade, thereby extending the life of seals and gaskets, and are in strong demand for use in next generation bio-fuel engines. The new grade of Zetpol® is well suited to extrusion processing which is being leveraged to expand its usage in various hoses. Products using Zetpol® have also been well received by customers, and are being used increasingly as a replacement material for more expensive competitive rubber in Japan, Asia, Europe and North America.
Commercial production of the new Zetpol® started in November 2012 at Zeon's Kawasaki Plant and reached full-scale production in 2013.
② Synthetic Latex Business
Synthetic latex is liquid rubber that synthetic rubber dispersed in water. It is used to manufacture gloves, paper coating, textile processing, adhesives, paints, and cosmetic puffs, etc. Zeon has close to 90% share of NBR latex used in cosmetic puffs.
③ Chemical Products Business
Zeon produces C5 fraction by its unique in-house GPI method, and turn it into materials for adhesive tapes and hot melt adhesive traffic paint binder and a wide variety of other products.
<Specialty Material Business>
① Specialty Plastics and Electronic Materials
Zeon deals in high value added materials and parts that are created using its unique technologies including polymer design and processing technologies.
Cyclo-olefin polymer is thermoplastic polymer developed using raw material extracted from C5 distillate using GPI methods and synthesized with Zeon's own unique technologies. The commercial products are ZEONEX® and ZEONOR®.
ZEONEX® leverages its high transparency, low water absorption and low absorptive properties for use in camera and projector lenses and other optical applications, and in medical use containers including syringes and vials.
ZEONOR® leverages its high transparency, transferability, and heat resistance properties for use as transparent general use engineering plastics used in light guide plates, automobile parts, containers, discs and a wide range of other product applications.
ZeonorFilm® is the world's first optical film by the melt extrusion method from the cyclo-olefin polymer. It is excellent in optical properties, low water absorption / low moisture permeability, high heat resistance, low outgassing and dimensional stability. Not only for displays for LCD TV, smartphones and tablets, is it expected to be used in a wide range of applications such as digital signage in the future.
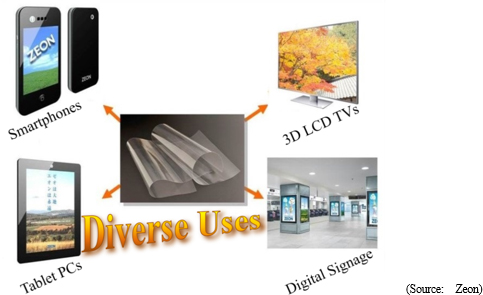
"Diagonally-stretched optical film" is also Zeon's world first development.
The OELD application as anti-reflection film is progressing, and demand for small- to medium-sized flat panel display applications is growing. In addition to the current plants in Takaoka and Himi (an annual output of 15 million square meters for optical film in total), the construction of a new plant in Tsuruga, Fukui Prefecture was completed in October 2013.
ZEOCOAT® is organic insulation material used in electronic devices such as cellphones, smartphones, and LCD televisions. ZEOCOAT® was successful in improving both the picture quality and reliability of displays because of its high transparency, extremely low water absorption and low gas generation properties. Zeon will aggressively expand its marketing efforts for OELDs, which will be thinner displays than LCD, thin-film transistors using new semiconductors, and flexible displays.
② Battery Materials
Zeon provides materials for lithium ion battery in this segment; anode / cathode binders, binder for functional layer (heat resistant separator), and sealant.
Currently, Li-ion batteries are widely used as a power source for mobile devices such as mobile phones and notebook computers. Due to the rapid popularization of smartphones, there is a strong demand for higher capacity batteries. Adoption for electric vehicles, including hybrid and plug-in hybrid cars, and industrial power sources (such as smart grids, etc.) also have begun, since it is lightweight, compact and can store a lot of energy. On the other hand, there was a problem that lifetime tends to decrease under high temperature usage.
The company has advanced the function of Li-ion battery binder and succeeded to develop an aqueous cathode binder, which greatly contributes to longer battery life. In addition, Zeon succeeded in commercializing anode binder, which can raise the storage capacity of Li-ion battery by 5% to 15%.
Zeon believes that its materials contribute to safety, long life and battery capacity increase of Li-ion batteries and contribute to the widespread of hybrid cars.
The company focused on the promising future of Li-ion batteries and worked on it for a long time. In this business segment for 2020, Zeon seeks to keep its top share in the Li-ion battery binder market, aims to expand the diffusion of new material functions that meet the needs of the application and propose functional materials to realize the next generation of new batteries.
③ Medical Device
The medical device market is relatively well insulated from fluctuations in the economy, and is anticipated to grow with the aging society in Japan and expansion in developing countries. Furthermore, medical device companies are subject to strict laws and regulations, and they need to submit approval applications to regulatory bodies. In addition, the need to develop relationships with healthcare professionals is critical and the subsequent high barriers to entry makes this a highly attractive market.
Along with the start of development of artificial kidneys in 1974, Zeon aggressively promoted its medical device business. In 1989, a subsidiary Zeon Medical Inc. was established to conduct development, manufacturing, sales and all other functions of the medical field for the Zeon Group. Zeon has shown bountiful development track record both in gastroenterology and cardiovascular area. The Offset Balloon Catheter as a means of differentiation in the gallstone removal process and with Japan's first biliary covered stent Zeostent Covered in the area of gastroenterology products, and the world's smallest diameter XEMEX IABP Balloon PLUS as a device to aid the heartbeat at times of acute myocardial infarction in the area of cardiovascular products.
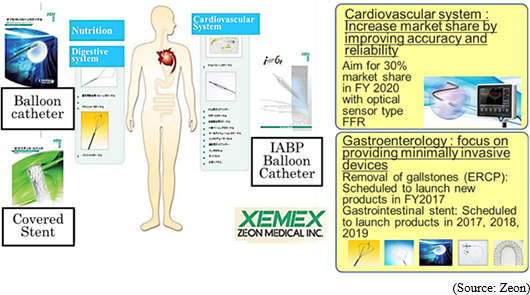
Currently Zeon is focusing efforts in the development of devices that eliminate gallstone pain by removal of gallstones. Zeon has a lineup of products that can remove gallstones ranging from extremely large stones to sludge and sand with products such as XEMEX Crusher Catheter, XEMEX Basket Catheter NT, Extraction Balloon Catheter, and is aiming at a 50% share of the gallstone removal market.
In March 2016, the Company launched the world's first optical sensor FFR device as a type of guide wire. Because it uses an optical fiber sensor, mistaken readings of blood pressure measurements rarely occur. The operability as a guide wire has also gained a high evaluation and Zeon is aiming for a 30% share of the Japanese market by 2020.
④ Chemical Business
Zeon deals in specialty chemicals that use derivatives from C5 fraction, such as synthesized fragrances for cosmetics and flavor used in foods, solvents and plant growth regulator. The Company holds the world's top share of the synthesized fragrances in green note. They provide a wide range of specialty products including ingredients for intermediary bodies used in medical and agricultural chemicals, alternative CFCs solvents, cleaning agents, urethane expanding agent, and functional ether agents.
【New Specialty Materials Development: ~Carbon Nano Tube (CNT)~ 】
Aggressive R&D activities have allowed Zeon to launch various new materials into the market, and particularly high expectation is in the development of "single-wall carbon nanotubes (CNT)".
① What is Single-Walled CNT?
Carbon Nanotubes (CNTs) are cylindrical nanostructure formed by hexagonal lattice of carbon atoms. In 1993, Sumio Iijima, Ph.D., head of the Applied Nanotube Research Center of the National Institute of Advanced Industrial Science and Technology (AIST), discovered this structure for the first time in the world and named Carbon Nanotubes (CNTs). CNTs are categorized into single-walled and multiple-walled CNTs. Multiple-walled CNT is relatively easy to manufacture and the developments for commercial applications already started.
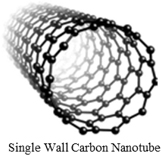
At the same time, single-walled CNT exhibits the following properties and is superior to multiple-walled CNT:
- 20 times stronger than steel
- 10 times more heat conductive than copper
- Half as dense as aluminum
- 10 times the electron mobility of silicon
- lightweight but highly flexible
- has extremely high electric-and heat-conductivity properties
Possible CNT applications are electrical conductivity assistance agent in Li-ion batteries, transparent conductive film used in electronic paper and ultra-thin touch panel because of its high elasticity and strength, and as a thermal interface material. Because of its ability to absorb a wide spectrum of light, practical applications of single-walled CNT are being promoted in the area of electromagnetic wave absorbing materials for use in a wide range of fields including energy, electronics, structural materials, and specialty materials.
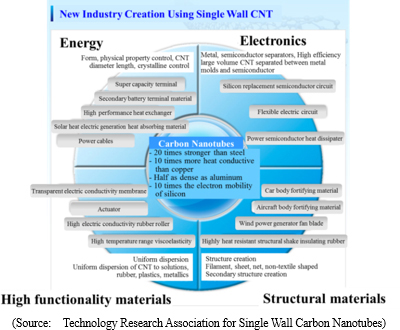
Conventional single-walled CNT has several major issues including high levels of impurities, low levels of productivity and high manufacturing costs, which are about several tens of thousands to hundreds of thousands of yen per gram.
② Zeon's Efforts and Position
Against this backdrop, the AIST and five companies* jointly established the technological consortium Technology Research Association for Single-Walled Carbon Nanotubes in May 2010 (*Zeon, NEC Corporation, Toray Industries, Teijin Limited, and Sumitomo Precision Products Co., Ltd.). The consortium aims at establishing technologies that are necessary for the commercialization of new products using single-walled CNT developed in Japan with its numerous superior qualities in response to the worldwide social demands to realize a low-carbon society.
Using the synthesizing technology super growth method developed by Dr. Kenji Hata (Ph.D.) of the AIST as a base, the above-mentioned consortium has been conducting R&D for mass production and application development for compound materials at a validation plant that was established in December 2010 on the premises of the Tsukuba Center of the AIST. Among the main reasons that the AIST Nanotube Application Research Center selected Zeon to become its partner were the impressive track record and results obtained by Kohei Arakawa, Zeon's former Managing Director, as a personnel in CNT R&D. Furthermore, the fact that the consortium director is Zeon President Furukawa reflects the importance of Zeon in this project to realize commercial applications of single-walled CNT.
③ Future Endeavors
Having established the mass production technology based on the super growth method, Zeon completed the CNT production facility and started mass production, the first in the world in November 2015 in its Tokuyama plant at Shunan-city, Yamaguchi Prefecture.
Zeon is the only company in the world that has established mass production technologies for single-wall CNT. In addition to those companies within the consortium mentioned above, about 100 companies around the world request for its product samples. Consequently, shipments of samples have already begun. Zeon has also begun to propose practical applications of this product.
At the same time, single-wall CNT is a type of nanomaterial that is extremely small and fiber shape. Therefore, there is a concern that it may have some impact upon biological processes depending upon its size and shape. Currently, the AIST is conducting standardization of the evaluation process, and activities for the OECD endpoint measurement are being conducted, with global standardization and legal and regulatory aspects being considered.
<Other Business>
The combination liquid for Reaction Injection Molding (RIM) and molded items using the ingredient dicyclopentadiene (DCPD) as a raw material.
(Characteristics and Strengths)
1. World's Leading Creative Technology Development Capability
The GPB method used to manufacture butadiene from C4 fraction is the most important development in Japan's postwar history of chemicals, and is licensed to 49 plants in 19 countries around the world.
In addition, the Mizushima Plant is the world's only plant with GPI method to extract high-purity isoprene and other effective substances from C5 fraction. This Zeon's GPI method is a completely unique technology, which is not provided to other companies. Zeon is able to acquire basic ingredients used in synthesized fragrances and petroleum resin.
These two technologies represent the creative technological capabilities that are among the strengths of Zeon. They also are highly regarded and have received numerous awards in the global markets. With regard to technologies, Zeon has received 48 awards since 1960 including the GPB and GPI methods, in addition to 26 awards since 1982 for its environment conservation and safety efforts.
2. High Worldwide Share
Zetpol®, ZEONEX®, and ZEONOR® are representative of the products born from Zeon's highly creative technologies, which have allowed it to acquire high shares of worldwide markets. In addition, their Leaf alcohol for in cosmetics and food flavorings and NBR latex for cosmetic puffs have the world's top share.
3. R&D Structure that Continues to Yield Creative Technologies
Zeon seeks to conduct R&D activities based upon its basic corporate philosophy of “developing creative technologies in special fields of strength that enables Zeon to contribute to society by generating the world's leading businesses."
The Company's main R&D center is located in Kawasaki City, Kanagawa Prefecture. Zeon has also established the Precision Optics Laboratory and Medical Laboratory at the Takaoka Plant, the Chemical Product Research Facility at the Yonezawa Plant and at the Mizushima Plant and the Toner Research Facility at the Tokuyama Plant for more efficient R&D activities to be conducted closer to the manufacturing sites. The technical support bases are in the U.S., Europe, Singapore, and China.
The R&D personnel are never satisfied with the current conditions, and always keep conscious of the threat that their competitors pose in their research activities. Furthermore, Zeon bases its valuation on a positive point awarding system that places high priority on speed and creativity. R&D expenses were formerly measured as a percentage of sales, but now it has established an annual value amount of ¥12.0 ~ ¥13.0 billion as an investment budget to ensure that stable R&D activities can be maintained in the future.