Bridge Report:(1433)BESTERRA 1H of Fiscal Year Ending January 2025
![]() President Yutaka Honda | BESTERRA CO., LTD (1433) |
![]() |
Company Information
Market | TSE Prime Market |
Industry | Construction business |
President | Yutaka Honda |
HQ Address | Kiba Park Building, 3-2-6 Hirano, Koto-ku, Tokyo, Japan |
Year-end | End of January |
Homepage |
Stock Information
Share Price | Share Outstanding (End of the term) | Market Cap. | ROE (Act.) | Trading Unit | |
¥909 | 8,990,200 shares | ¥8,154 million | 5.5% | 100 shares | |
DPS (Est.) | Dividend Yield (Est.) | EPS (Est.) | PER (Est.) | BPS (Act.) | PBR (Act.) |
¥20.00 | 2.2% | ¥54.17 | 16.8 x | ¥461.31 | 2.0 x |
*The share price is the closing price on September 13. Share outstanding, DPS, and EPS are from the financial results for the second quarter of the fiscal year ending January 2025. ROE and BPS are actual results in the previous fiscal year.
Consolidated Earnings
Fiscal Year | Net Sales | Operating Income | Ordinary Income | Net Income | EPS | DPS |
Jan. 2021 (Actual) | 3,682 | 124 | 212 | 142 | 17.33 | 16.00 |
Jan. 2022 (Actual) | 5,966 | 488 | 721 | 1,391 | 165.48 | 16.00 |
Jan. 2023 (Actual) | 5,458 | -215 | -94 | -64 | -7.33 | 20.00 |
Jan. 2024 (Actual) | 9,394 | 246 | 407 | 231 | 26.08 | 20.00 |
Jan. 2025 (Forecast) | 11,000 | 500 | 650 | 480 | 54.17 | 20.00 |
* The forecasted values were provided by the company. Unit: million yen. Net income is profit attributable to owners of parent.
This Bridge Report introduces the earning results for the first half of the fiscal year ending January 2025 and other information of BESTERRA CO., LTD.
Table of Contents
Key Points
1. Company Overview
2. 1H of Fiscal Year Ending January 2025 Earnings Results
3. Fiscal Year Ending January 2025 Earnings Forecasts
4. The medium-term management plan, “Action Plan for Decarbonization 2025”
5. Conclusions
<Reference: Regarding Corporate Governance>
Key points
- In the first half of the fiscal year ending January 2025, sales increased 73.3% year on year to 5,767 million yen. Sales increased significantly, exceeding the company's forecast (5.5 billion yen) disclosed in June due to the acquisition of new clients and the steady progress of large-scale demolition projects received in the previous fiscal year as a result of the strengthening of the company's organizational structure. This was a record high for the first half of a fiscal year. Operating income was 211 million yen (an operating loss of 61 million yen in the same period of the previous year). The operating income absorbed the increase in SG&A expenses caused by temporary demolition project losses recorded in the first quarter and active research and development investments for the future. The company substantially exceeded its forecast disclosed in June due to the steady progress of demolition projects and a significant decrease in the impact of unprofitable demolition projects, as the company strengthened its demolition system as a result of its aggressive recruiting activities. The company plans to pay a dividend of 10 yen per share at the end of the first half, which is in line with the company's forecast.
- The full-year forecast was revised upwardly in June. Sales are expected to increase 17.1% year on year to 11 billion yen, and operating income to rise 102.5% year on year to 500 million yen. In the first half of the year, they kept receiving many business inquiries, because of the abundant demand for plant demolition work. In the hiring of human resources, the most important issue for the company, aggressive recruiting activities have been successful, and the company has made steady progress in establishing a framework for further sales expansion. As a result, the sales and profit in the first half exceeded the company's forecast announced in June. For the full year, the company has not revised its sales and operating income forecasts, although it continues to see abundant demand for demolition work and maintains a large backlog of orders. The company upwardly revised its ordinary income and net income forecasts, reflecting gains on the sale of shares and other factors. The company plans to pay a dividend of 10 yen/share at the end of the fiscal year and a full-year dividend of 20 yen/share, as forecast at the beginning of the fiscal year. Payout ratio is expected to be 36.9%.
- In the first half of the year, sales increased significantly, even exceeding the company's forecast disclosed in June, and profit improved significantly. Although the company did not revise its full-year forecasts for sales and operating income at the time of the announcement of the earnings for the first half, it seems that there is considerable room for improvement. In addition, operating income in the second quarter (May-July) was 194 million yen, showing a significant increase from 17 million yen in the first quarter (February-April). This was due to the decrease in the impact of unprofitable orders and steady progress in demolition projects. In the previous report, we stated that "improving profit margin is a challenge," and it appears that profit margin has actually improved and is expected to expand in the future as the sales of unprofitable orders decline further. It can be said that the company is entering a stage of full-fledged profit growth. The company appears to be making progress in developing an organizational structure that can withstand significant growth in sales through steady personnel recruitments.
- While “decarbonized demolition solutions (innovation through construction methods),” which is the core strategy of the “Action Plan for Decarbonization 2025,” demonstrated strong growth, progress in “DX plant solutions (innovation through IT)” was slow, but the potential demand is large in both areas, with the business environment being favorable. Under the new management structure, the company will focus on further improving profit margin while leveraging the company's strengths to develop the market at the expected speed.
1. Company Overview
As a specialist in plant dismantlement, BESTERRA manages the dismantlement of plants (metal structures) for iron-making, power generation, gas, petroleum, etc. Its core competence is “the method and technology for dismantling plants,” and it has many patented methods including international patents. The company concentrates its managerial resources on engineering (proposal, design, and work planning) and management (supervision and work management), and outsources actual dismantlement work to its affiliates, and so it does not own heavy machinery or construction teams (the risk of owning assets can be avoided), and it is unnecessary to procure materials, etc. and make transactions for material production (the inventory risk can be avoided).
In addition to the company, the group has acquired Hiro Engineering, which provides human resource services for design work, etc., 3D Visual KK, which handles 3D scan modeling and design work, and Yazawa Co., Ltd., which owns advanced technologies for removing asbestos as consolidated subsidiaries. Additionally, in August 2023, the company has also acquired Oda Corporation Co., Ltd., which mainly maintains work and main frame construction work, and its subsidiary, TOKEN Co., Ltd. as consolidated subsidiaries. As of the end of January, there were five consolidated subsidiaries.
The corporate name “BESTERRA” was coined by combining the English word “Best (the superlative of ‘good’)” and the Latin word “Terra (the earth),” and infused with the ambition to “create the best earth.” By developing an integrated system for dismantling and recycling, the company aims to actualize an advanced recycling society and contribute to the earth environment.
1-1 Corporate ethos and the code of conduct
Under the corporate philosophy of "we will contribute to the global environment with flexible thinking, creativity, and techniques," the company's mission is to "realize the BEST (highest) TERRA (earth)" and "contribute to the development of an advanced recycling-oriented society (development of vein industries).”
The company has also established a "Basic Sustainability Policy" to contribute to the realization of a sustainable society.
◎ Basic Sustainability Policy
We, Besterra, are committed to both "realization of an advanced recycling-oriented society" and "sustainable corporate growth" based on our corporate philosophy of "We will contribute to the earth environment with our flexible way of thinking, creativity, and technologies using these concepts."
1-2 Characteristics of the business
The company has a single segment consisting of demolition and maintenance business. For others, it engages in the human resource service business and the 3D scan, modeling, and design business. In the fiscal year ended January 2024, demolition and maintenance business accounted for 97.3% of total sales.
Demolition and maintenance business
In the demolition and maintenance business, the company works mainly on all types of plants in the fields of ironmaking, electric power, gas, petroleum, and petrochemicals, etc. The company offers services on overall engineering processes including proposals, designing, work planning, outsourcing/arrangement of equipment and materials, supervision, safety management, cost management, financial management, and handling of governmental procedures. It focuses on designing its unique demolition technologies and supervising demolition works based on demolition plans and uses specialized subcontractors for demolition works.
The clients for plant dismantlement are leading companies that own plants for ironmaking, electric power, gas, petroleum, etc. In most cases, the equipment installation companies of the corporate groups of clients or leading general contractors are entrusted with dismantlement, and then BESTERRA serves as the primary or second-tier subcontractor.
Also, in the plant dismantlement business, BESTERRA receives valuable materials generated through dismantlement, such as scrap, and sells them to scrap handlers. Accordingly, the company estimates the value of valuable materials while comprehensively considering the material, quantity, price (market price of each material, such as iron, stainless steel, and copper), etc. and negotiates with clients about the fee for dismantlement work. In accounting, the gain from sale of valuable materials is included in revenue from dismantlement work and posted as part of sales from completed dismantlement work. In some cases, contractors (clients) dispose of (sell) scrap, etc. by themselves.
Furthermore, Oda Corporation Co., Ltd. and TOKEN Co., Ltd., which became consolidated subsidiaries in August last year, will be part of the demolition and maintenance business, with maintains work and main frame construction work for various plants as their core business.
*Two standards for posting revenue and seasonality of revenue posting of the company
The standards for posting revenue from contracts can be classified into the completed contract method, in which revenue is posted when works are completed, and the percentage-of-completion method, in which revenue is posted according to the progress of works. The company basically applies the percentage-of-completion method to large-scale projects whose period exceeds 3 months from the term ended January 2023 (the completed contract method is applied to projects that do not meet the aforementioned criteria). The timing of posting revenue (the completion of demolition work) from works for which the completed contract method is used is often affected by the capital investment plans of clients. In the case of BESTERRA, revenue tends to be posted in the first quarter (February to April) and the fourth quarter (November to January) (the seasonality of revenue posting). However, the variation in quarterly performance may mislead investors, so the company is expanding the scope of application of the percentage-of-completion method step by step, to equalize the timings of revenue posting.
Others
In response to the chronic shortage of skilled construction workers, the company began providing human resource services in January 2013, and in March 2018, it made Hiro Engineering, which handles human resource services such as design work, a subsidiary. In January 2015, the company began offering a 3D measurement service as well. It established 3D Visual KK in December 2019, and 3D scan modeling and design business was transferred from INTER ACTION Corporation (securities code: 7725) in February 2020.
1-3 Strengths: an excellent client base, efficient dismantlement management based on plenty of experience, and intellectual property, such as patented methods
The strengths of the company are excellent client assets, efficient dismantlement management based on plenty of experience, and intellectual property, such as patented methods. The clients are basically engineering subsidiary companies of leading companies in ironmaking, electric, gas, coal oil fields, and major general contractors, which are excellent clients with no credit concerns. The clients of the leading companies highly evaluate the company’s total management (low cost and high efficiency) of plant dismantlement that it cultivated experiences for over 40 years. Another strength is the various technologies and know-how that the company has accumulated through environmental protection construction projects, etc., which have become its actual and potential intellectual property, including the recycling of waste materials.The company operates business under the concepts of "unbreakable by its creators (new ideas)," "the only one company specializing in plant dismantling," and "asset-light management.”
Patented methods, etc.
“Apple peeling demolition method” and fusing robot “Ringo☆Star”
The “apple peeling demolition method” is a method of dismantling a large spherical tank, such as gas holders and oil tanks, by cutting it in spirals from the center of the ceiling of the enclosure part. The cut part spirals down to the ground gradually under the force of the earth’s gravity (natural energy). The method enjoys superiority in a work period, cost, and safety, and has considerable competitive advantages, realizing “greater promptness, higher cost efficiency, and added safety.” Furthermore, the company offers a robot for the fusing process, “Ringo☆Star,” which automates the “apple peeling demolition method.” (The company is also working to expand the range of applications for “Ringo☆Star” by developing a new attachment).
Environment-related methods
The company has cultivated experiences and business results of a multitude of environment-related demolition works, using the “fireless methods” which do not require the use of fire. For example, although polychlorinated biphenyls (PCBs) are considered as a toxic substance and therefore totally abolished today, it had been used for many years in transformers and condensers because of its excellent thermal stability and chemical stability (electric insulation characteristics). In many cases, transformers and condensers are disposed of in conjunction with plant demolition works; however, because PCBs gasify when they are treated at the high temperature, posing a risk of inhaling the gas so generated, any firearms (such as gas cutting machines) cannot be used in demolition and withdrawal involving PCBs. The company is skillful at fireless and quasi-fireless methods using saber saws (which cut off objects with their saw blades moving in a reciprocating manner) that can cut off objects thicker than the thickness, which, in the industry, had been considered impossible to cut, through numerous devices, including measures against seizure of motors and recycling of blades. BESTERRA has applied for joint patents with Hitachi Plant Construction, Ltd. for a transformer dismantling method, a transformer dismantling jig, and a cutting device for dismantling a transformer.
Windmill demolition works
The number of power-generating wind turbines continues to increase by about 20% annually worldwide, but the demand for dismantling is expected to increase in the future due to wear and tear and economic obsolescence. According to the company's data, the global wind power generation amount has continued to grow at an annual rate of about 20%, reaching 486,790 MW (about 340,000 onshore units and about 4,000 offshore units). In Japan, there were 2,574 wind turbines as of the end of 2021, mostly onshore, but the trend is shifting toward offshore wind power. Meanwhile, as the useful life is approximately 15 to 20 years, and the windmills for power generation established in the early stage are reaching the application limit. Moreover, not a few plants need to be dismantled due to damage or fatal failure caused by thunderbolts or typhoons.
How to knock down a power-generating wind turbine (international patent application)
Dismantling of windmills is usually done using scaffolding erected on the outside of the supports. As some windmills have been built in mountain districts and on the sea, demolition of them is highly difficult. The company has devised a method for dismantling wind turbines that does not require scaffolds and has already acquired a domestic patent for “Method of knocking down a power-generating wind turbine.” International patents are pending for “Method of knocking down towering structures using their bases” and “Method for dismantling tower-shaped equipment for wind power generation.” Safety of workers can be improved dramatically, and the work period can be shortened by using these patent-based methods.
Pursuit of the value of the 3D business
Using services such as layout simulation, strain/bending/torsion measurement, comparison of structures before and after improvement, and video walkthroughs, the company converts physical data taken when plants were established (more than 30 years ago) into the latest 3D data and uses that to provide detailed information about the dismantling process. They also provide unique 3D measurement services for dismantling work using the latest measuring technology and simulation systems that are capable of drawing data as 2D diagrams, handling BIM/CIM modeling, Perfect 3D, and 3D printing, etc.
“Visualize” the dismantling process
Layout simulation | The equipment models produced with 3D CAD are placed in 3D data, and the replacement of equipment can be simulated. By moving the equipment models, it is possible to check how they interfere and collide with one another. |
Strain, bending, and torsion measurements | It is possible to measure changes in shapes. This is useful for diagnosing frameworks tentatively, to check whether a building got distorted due to an earthquake, deterioration, etc. |
Comparison of structures before and after installation
| The shapes of equipment that changes due to heat and vibration, such as pipes, conveyors, and furnaces, at the time of installation and after operation are compared. With 3D data, it is possible to grasp overall changes intuitively. |
Video walkthroughs
| Walk-through videos are produced by using synthesized point cloud data. These videos can be utilized for presentations and publicity videos regarding dismantlement plans and real estate information. |
Unique 3D measurement service
Draws a two-dimensional diagram | The 3D CAD models based on point cloud data are converted into drawings. It is also possible to produce drawings directly from point cloud data in a simple manner. |
Handles BIM/CIM modeling | Modeling is conducted with 3D CAD based on point cloud data. It is possible to produce models of the parts that require construction or renovation as BIM (building information modeling) data. |
Perfect 3D | This is a large-scale 3D data measurement service combining automobile-based MMS (mobile mapping system), airborne laser measurement, water area measurement, etc. |
3D printing | After modeling with point cloud data, data are processed and deformed so that they can be shaped with a 3D printer. It can produce fine structures with a lamination pitch of 15 μm. |
1-4 ROE analysis
| FY 1/18 | FY 1/19 | FY 1/20 | FY 1/21 | FY 1/22 | FY 1/23 | FY 1/24 |
ROE (%) | 11.7 | 23.8 | 2.3 | 5.6 | 40.6 | -1.5 | 5.5 |
Net Income to Sales Ratio (%) | 5.87 | 12.62 | 1.75 | 3.87 | 23.32 | -1.18 | 2.46 |
Asset Turnover Ratio (Times) | 1.11 | 1.08 | 0.72 | 0.67 | 0.80 | 0.63 | 0.97 |
Leverage (Times) | 1.80 | 1.75 | 1.85 | 2.14 | 2.19 | 2.01 | 2.28 |
The ROE in the fiscal year ended January 2024 is higher than that in the previous fiscal year, but it is 5.5%. The new medium-term management plan, “Action Plan for Decarbonization 2025” (see below), targets “an ROE of 13% or higher in fiscal year ending January 2026.”
2. 1H of Fiscal Year Ending January 2025 Earnings Results
2-1 Consolidated results
| FY 1/24 1H | Ratio to sales | FY 1/25 1H | Ratio to sales | YoY | Company forecast ratio |
Sales | 3,328 | 100.0% | 5,767 | 100.0% | +73.3% | +4.9% |
Gross profit | 470 | 14.1% | 960 | 16.7% | +104.2% | - |
SG&A expenses | 531 | 16.0% | 749 | 13.0% | +40.9% | - |
Operating income | -61 | -1.8% | 211 | 3.7% | - | +111.0% |
Ordinary income | -9 | -0.3% | 258 | 4.5% | - | +72.0% |
Net income | -28 | -0.9% | 127 | 2.2% | - | +27.2% |
*Unit: million yen. Net income is net income attributable to owners of the parent company. The company forecasts are the forecasts announced in June 2024.
Sales increased significantly, moving into the black
Sales increased 73.3% year on year to 5,767 million yen. Sales grew significantly, exceeding the company's forecast (5.5 billion yen) disclosed in June, thanks to the acquisition of new clients and the steady progress of large-scale demolition projects ordered in the previous fiscal year as a result of the strengthening of the company's organizational structure. This was a record high for the first half of a fiscal year. Sales in the second quarter (May-July) usually drop, but this year, sales remained large despite declining from the first quarter.
Operating income increased 272 million yen year on year to 211 million yen (a loss of 61 million yen in the same period of the previous year). The operating income absorbed the increase in SG&A expenses caused by temporary demolition work losses recorded in the first quarter and active research and development investments for the future. The company substantially exceeded its forecast disclosed in June as a result of the positive results of aggressive recruiting activities, which strengthened the demolition system, the steady progress of demolition projects, and a significant decrease in the impact of unprofitable demolition projects. Ordinary income was 258 million yen (a loss of 9 million yen in the same period of the previous year), and net income was 127 million yen (a loss of 28 million yen in the same period of the previous year), both of which exceeded the company forecast disclosed in June.
The company will pay a dividend of 10 yen/share, in line with its forecast.
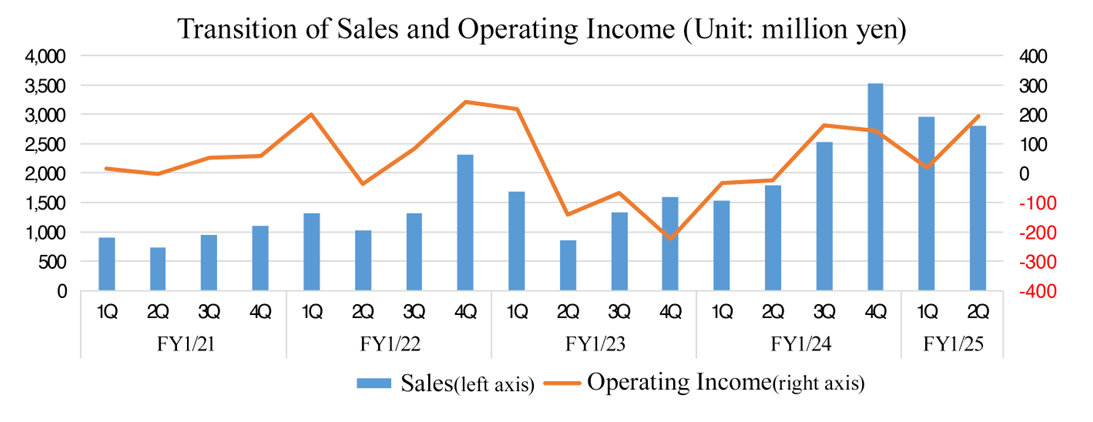
The number of completed works (rough estimates)
| FY 1/24 1H | Composition ratio | FY 1/25 1H | Composition ratio | YoY |
Electric power | 386 | 12% | 1,687 | 30% | +337% |
Steelmaking | 1,189 | 37% | 1,068 | 19% | -10% |
Petroleum/ petrochemical | 1,189 | 37% | 1,855 | 33% | +56% |
Gas | 64 | 2% | 56 | 1% | -13% |
3D | 64 | 2% | 56 | 1% | -13% |
Environment | 289 | 9% | 225 | 4% | -22% |
Others | 32 | 1% | 675 | 12% | - |
Total of completed works | 3,213 | 100% | 5,622 | 100% | +75% |
*Unit: million yen. Prepared by Investment Bridge Co., Ltd. based on company data.
The amount of completed demolition projects increased significantly. The electric power field accounted for a high proportion of the total number of projects due in part to significant progress in the demolition of power plants and substations. Large-scale orders received by the company as a prime contractor are progressing steadily in the electric power, petroleum, and petrochemical fields. Thus, the company completed demolition projects in the electric power, steelmaking, and petroleum and petrochemical fields, resulting in a balanced composition.
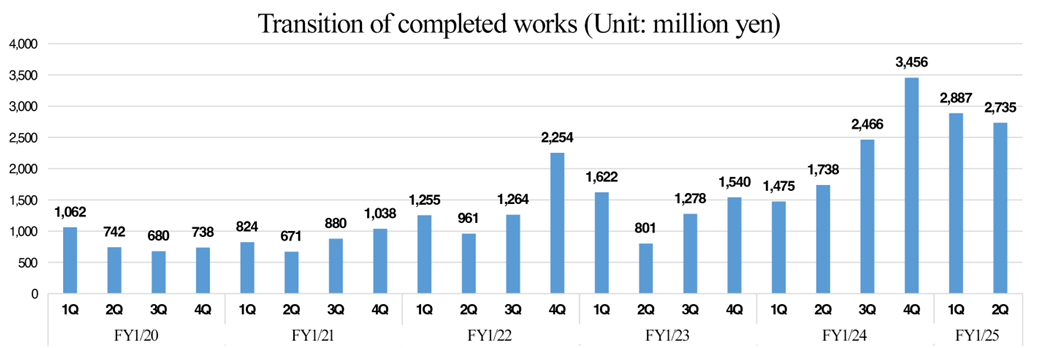
The amount of completed demolition projects tend to be small in the second quarter of every fiscal year. The amount of completed demolition projects in the second quarter of the fiscal year ending January 2025 was at the same level as that in the first quarter, although affected by seasonal factors. The company plans to increase the amount of completed demolition projects in the fourth quarter as it has done in previous years.
Breakdown of SG&A
| FY 1/24 1H | Ratio | FY 1/25 1H | Ratio | YoY | Major change factors |
Personnel expenses | 298 | 9.0% | 361 | 6.3% | +21.1% | Increase of employees |
R&D expenses | 0 | - | 35 | 0.6% | - | AI Development Project, Robot Development, AUSE function development |
Fees and compensation paid | 50 | 1.5% | 93 | 1.6% | +87.0% | System costs, marketing cooperation expenses |
Recruiting expenses | 29 | 0.9% | 29 | 0.5% | +1.6% | Advertising media, introduction commissions |
Others | 153 | 4.6% | 227 | 3.9% | +48.4% | Amortization of goodwill, etc. |
Total SG&A expenses | 531 | 16.0% | 749 | 13.0% | +40.9% | An increase due to making Oda Corporation a subsidiary Approx. 108 million yen |
*Unit: million yen. Ratio is ratio to sales.
SG&A expenses have increased due to the acquisition of Oda Corporation as a subsidiary. In addition, spending on R&D for AI development, robot development, etc., and system costs to improve operational efficiency are increasing.
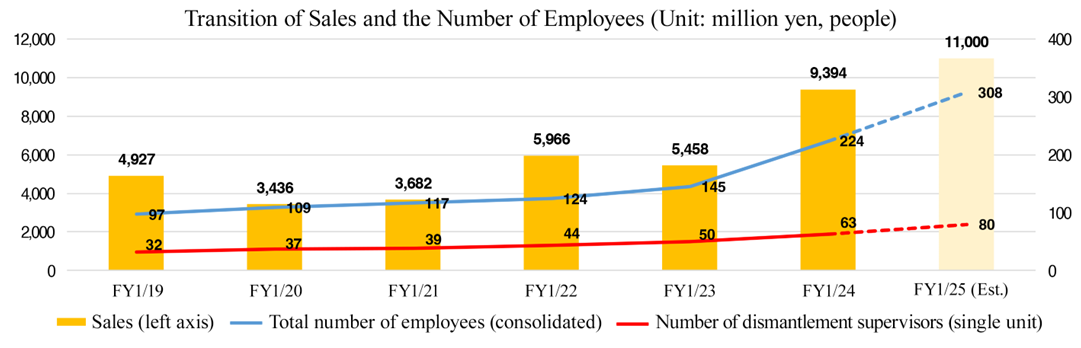
The number of demolition supervisors increased by 12 from the beginning of the fiscal year (16 hired) to 75. The company plans to continue to strengthen its structure for further sales expansion by increasing the number of demolition support units that provide support for demolition planning and demolition management.
2-2 Orders received and the backlog of orders
| FY 1/24 1H | FY 1/25 1H | YoY |
The backlog of orders at the beginning of the term | 3,352 | 7,087 | +111.4% |
The amount of works received | 8,822 | 4,710 | -46.6% |
The amount of completed works | 3,213 | 5,622 | +75.0% |
The backlog of orders at the end of the term | 8,960 | 6,174 | -31.1% |
*Unit: million yen
The amount of orders received decreased from the same period of the previous year when the company received orders for long-term, large-scale projects. Still, the number of business inquiries is extremely favorable in all industries. As a result of steady recruiting activities, the demolition system has been strengthened, and a framework has been put in place to deal with the ample order backlog.
Orders received by sector (Amounts are approximate.)
| FY 1/24 1H | Ratio | FY 1/25 1H | Ratio | YoY |
Electric power | 1,523 | 17% | 1,235 | 20% | -19% |
Steelmaking | 4,211 | 47% | 3,087 | 50% | -27% |
Petroleum/ petrochemical | 2,778 | 31% | 1,544 | 25% | -44% |
Environment | 448 | 5% | 123 | 2% | -72% |
Other | 0 | 0% | 185 | 3% | - |
Total order received | 8,960 | 100% | 6,174 | 100% | -31% |
*Unit: million yen
The steelmaking industry accounts for a higher percentage of the order backlog due to the long-term large demolition orders received in the previous fiscal year. While making steady progress in the large-scale demolition projects from the previous fiscal year, the company continues to receive orders for large-scale projects in all fields.
2-3 Financial condition and cash flow(CF)
Financial condition
| January 2024 | July 2024 |
| January 2024 | July 2024 |
Cash | 1,444 | 2,194 | Payables | 1,631 | 1,298 |
Trade receivables | 4,648 | 4,737 | Borrowings and Bonds | 4,292 | 5,344 |
Current Assets | 6,292 | 7,325 | Liabilities | 6,783 | 7,809 |
Investments, Others | 3,960 | 4,159 | Net Assets | 4,095 | 4,264 |
Noncurrent Assets | 4,586 | 4,749 | Total Liabilities, Net Assets | 10,879 | 12,074 |
*Unit: million yen. Trade receivables include notes and accounts receivable, accounts receivable from completed construction contracts, and contract assets.
Total assets increased 1.1 billion yen from the end of the previous fiscal year to 12 billion yen, mainly due to an increase in cash and deposits in preparation for payments to partner companies.
Total liabilities increased 1.0 billion yen year on year to 7.8 billion yen, mainly due to an increase in short-term loans.
Net assets increased by 100 million yen to 4.2 billion yen due to the revaluation of investment securities and accumulation of net income.
Capital-to-asset ratio dropped 2.3 points from the end of the previous term to 35.3%.
Cash Flow(CF)
| FY 1/24 1H | FY 1/25 1H | YoY |
Operating Cash Flow(A) | -450 | -199 | +251 |
Investing Cash Flow(B) | 1 | -12 | -14 |
Free Cash Flows (A + B) | -449 | -212 | +237 |
Financing Cash Flow | 676 | 962 | +285 |
Cash and Equivalents at Term End | 1,565 | 2,194 | +629 |
*Unit: million yen
The cash outflow from operating activities shrank due to the improvement in accounts receivable, and the deficit in the free CF decreased.
The cash position improved due to an increase in cash and cash equivalents in preparation for payments to partner companies.
2-4 Topics
(1) Expansion into the Overseas Plant Dismantling Market
The company agreed to enter into a strategic partnership with DENZAI K.K. to expand its demolition business for overseas plants. Through mutual cooperation, both companies aim to strengthen their foothold in the overseas plant market and further expand their businesses
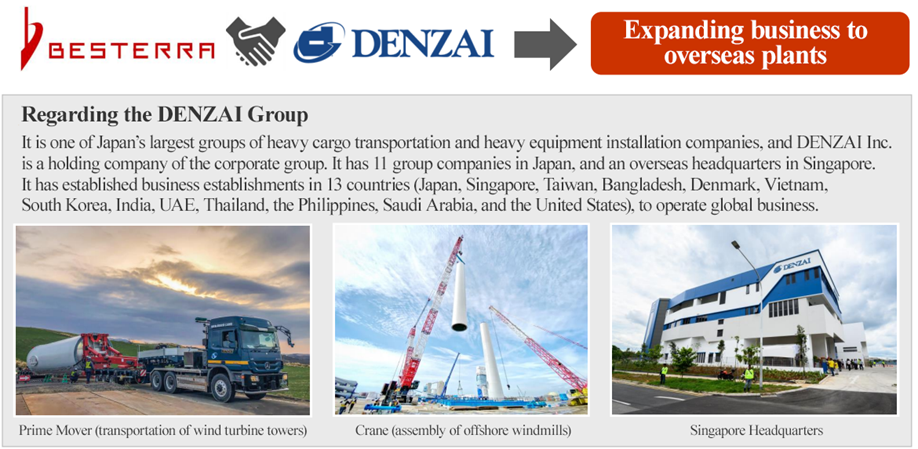
(Source: The company)
(2) Initiatives toward decarbonization in the dismantling business
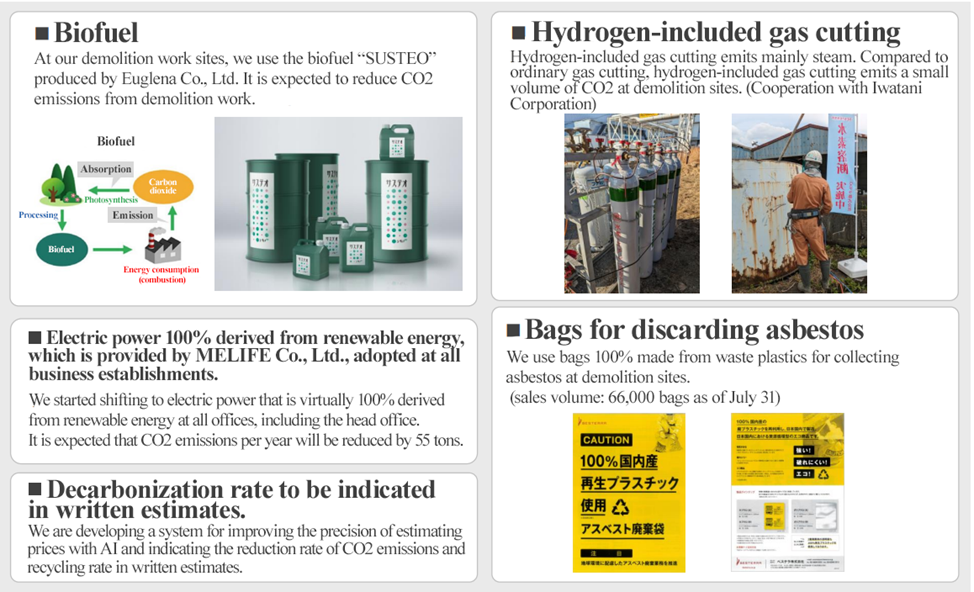
(Source: The company)
(3) CAD add-on software (Subsidiary: 3D Visual, Inc.)

(Source: The company)
3. Fiscal Year Ending January 2025 Earnings Forecasts
Full-year consolidated earnings forecast
| FY 1/24 Act. | Ratio to sales | FY 1/25 Est. | Ratio to sales | YoY | Initial forecast |
Sales | 9,394 | 100.0% | 11,000 | 100.0% | +17.1% | 10,000 |
Operating income | 246 | 2.6% | 500 | 4.5% | +102.5% | 420 |
Ordinary income | 407 | 4.3% | 650 | 5.9% | +59.5% | 520 |
Net income | 231 | 2.5% | 480 | 4.4% | +107.7% | 350 |
*Unit: million yen
Forecast for increased revenues and significant profit growth
Sales are expected to increase 17.1% year on year to 11 billion yen, and operating income to increase 102.5% year on year to 500 million yen. The initial forecast was revised upwardly in June, as shown above. No revision has been made this time. The company revised its ordinary income forecast to 650 million yen from the revised forecast of 600 million yen in June and its net income forecast to 480 million yen from 400 million yen to reflect gains on the sale of shares and other factors.
Due to a strong demand for plant dismantling projects in the first half of the year, the number of business inquiries remained large. Through proactive sales activities to acquire new customers, the company successfully secured new clients and projects as a prime contractor in the electric power, petroleum, and petrochemical sectors. Since the first quarter, the company has been working on projects with an abundant order backlog. In large-scale projects ordered in the previous fiscal year and high-profit projects ordered this fiscal year, the company has been striving to improve profitability by shortening demolition periods through innovations in dismantling methods and process management. In the hiring of human resources (demolition supervisors), the company's most important issue, its aggressive recruitment activities have been successful, with 12 hires as of September, compared to its target of 17 hires. As a result, in this favorable order receiving environment, the company was able to support demolition orders received by increasing the number of demolition planning and demolition management support staff. As a result, the sales and profit in the first half exceeded the forecasts announced in June. However, the company did not revise its full-year forecasts for sales and operating income, taking into account uncertainties such as the rate of progress of demolition projects despite abundant demand for demolition work and an ample order backlog.
The company plans to pay a year-end dividend of 10 yen per share, like in the previous year, for a total annual dividend of 20 yen per share, as forecast at the beginning of the fiscal year. Payout ratio is expected to be 36.9%.
4. The medium-term management plan “Action Plan for Decarbonization 2025”
In the term ended January 2023, both sales and profit were significantly below initial forecasts. Thus, the company has formulated a new medium-term management plan, Action Plan for Decarbonization 2025, in place of the Medium-Term Management Plan 2025, which it has been implementing since the term ended January 2022. Under the new management system, the company will position the term ending January 2024 to the term ending January 2026 as a turning point for further growth. The company decided to improve profitability by promoting decarbonization-oriented management and reforming its corporate culture, taking into account changes in the business environment in Japan and within this industry.
4-1 Business environment analysis
(1) Japan
Toward the realization of carbon neutrality in 2050, the demolition market is expected to expand further, with demolition progressing mainly for buildings in which 50 years or more have passed since their construction.
In the electric power market, the diversification of the energy mix will be significantly reviewed toward 2030, and a significant reduction of low-efficiency coal-fired power plants is expected.
In the steel manufacturing market, due to the progress of corporate restructuring and aging, it is necessary to remove and repair redundant facilities.
In the petroleum and petrochemical markets, many industrial complexes were built during the high economic growth period. Therefore, it is expected that facilities will be upgraded and reorganized from the perspective of international competitiveness and excessive production capacity.
In other manufacturing markets, facilities are expected to be renovated and dismantled due to the evolution of technology known as the 4th industrial revolution and the impact of business rationalization due to changes in domestic supply and demand.
The company estimates the size of each market as follows.
Market | Size |
Electric power | About 13 trillion yen |
Steel | About 2 trillion yen |
Petroleum/Petrochemicals | About 8 trillion yen |
Other manufacturing industries | About 20 trillion yen + α |
*Company’s estimates
(2) Industry
The following changes in the business environment and needs can be seen.
Increase of separate orders for dismantling | When a client (facility owner) places an order with a company specializing in demolition, there are many cases in which the reliability of the demolition company as a new business partner becomes a problem, as it is necessary to place an order with a company that complies with all laws and regulations and meets the high safety standards of each plant. In order to receive direct orders, the demolition company needs to be a listed company with high creditworthiness and possesses technologies that do guarantee not only safe demolition but are also safe for the environment. In conventional plant demolition work, there were many cases in which a client (facility owner) ordered the demolition of old facilities and the construction of new ones together. Due to the increase in demolition work that does not involve renewal and the rising difficulty of demolition work due to various laws and regulations, the orders for demolition work to specialized construction companies are increasing.
|
Adopting computer-aided construction | Due to the labor shortage in the construction industry because of the declining birthrate and aging population, efforts to computerize construction have become an issue for the industry. |
New needs for decarbonized work | Clients (facility owners) in the manufacturing industry are demanding environmental considerations and improved recycling rates not only in the manufacturing process but also in construction. |
(3) Company’s strengths
The company has a superior position as a plant demolition specialist (a rich track record), technological capabilities (decarbonized demolition®, patented methods, technology development, initiatives for DX), business alliances (Solution-offering capabilities for the entire venous industry), reliability, comprehensive plant demolition management (demolition method proposals, complying with environment-related laws and regulations, ability to purchase valuable materials, appropriate treatment of industrial waste, ability to mobilize companies, etc.). In response to the above needs and changes, it will harness these strengths to capture demand.
4-2 Overview of Action Plan for Decarbonization 2025
(1) Basic policy
The company's basic policy is to improve profitability through decarbonization-oriented management and transformation of the corporate culture.
Seeing changes in the business environment as an opportunity, the company will promote decarbonization-oriented management and reform its corporate culture to improve profitability, and it has positioned the three years from the term ending January 2024 to the term ending January 2026 as a turning point toward further growth.
(2) Numerical targets
The group has set the following numerical targets.
The initial forecast for the fiscal year ending January 2026 calls for sales of 10 billion yen, an operating income of 1 billion yen, and a net income of 752 million yen. The company has revised both sales and profit from the original plan from time to time, including those in the fiscal year ending January 2025.
The company aims to recover ROE to double digits as soon as possible.
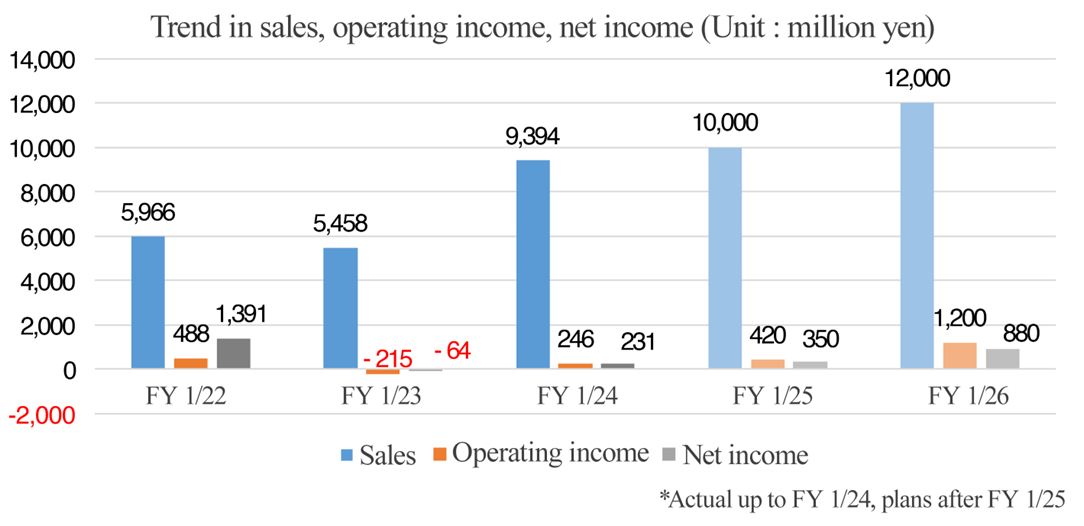
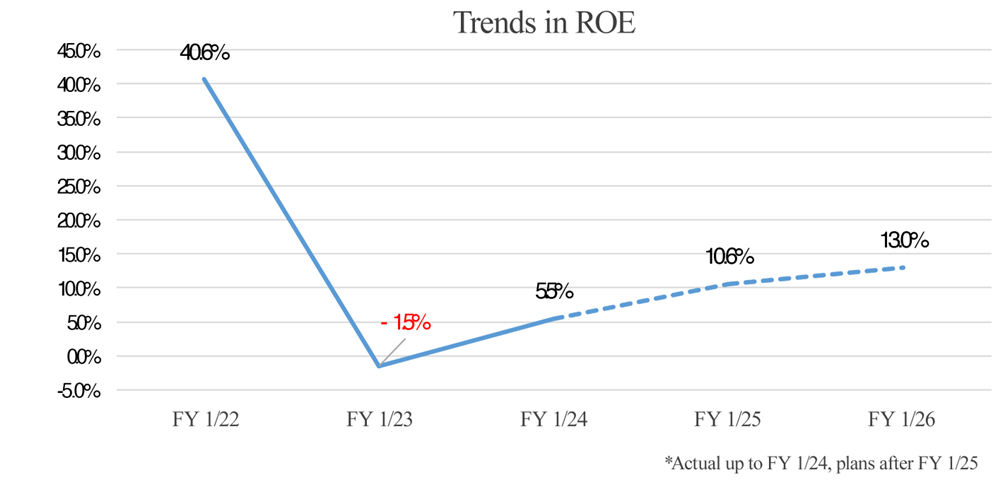
(3) Strategies and measures
To achieve the basic policy, the company will promote the following strategies and measures.
The three key strategies are decarbonized demolition solutions (innovation through demolition methods), DX plant solutions (innovation through IT), and personnel strategies (foundation for further innovation).
The company has newly established the Decarbonized Business Promotion Department in order to improve corporate value and brand through decarbonization-oriented management.
The company will promote "the development of demolition methods that contribute to decarbonized demolition®, the improvement of the reuse and recycling rate in demolition work, the reduction of GHG emissions and its visualization, and the creation of new businesses linked to decarbonization-oriented management.
①Overview of key strategies: Decarbonized demolition solutions
The company will develop various demolition methods that are environmentally friendly and provide pioneering demolition solutions that achieve decarbonized demolition.
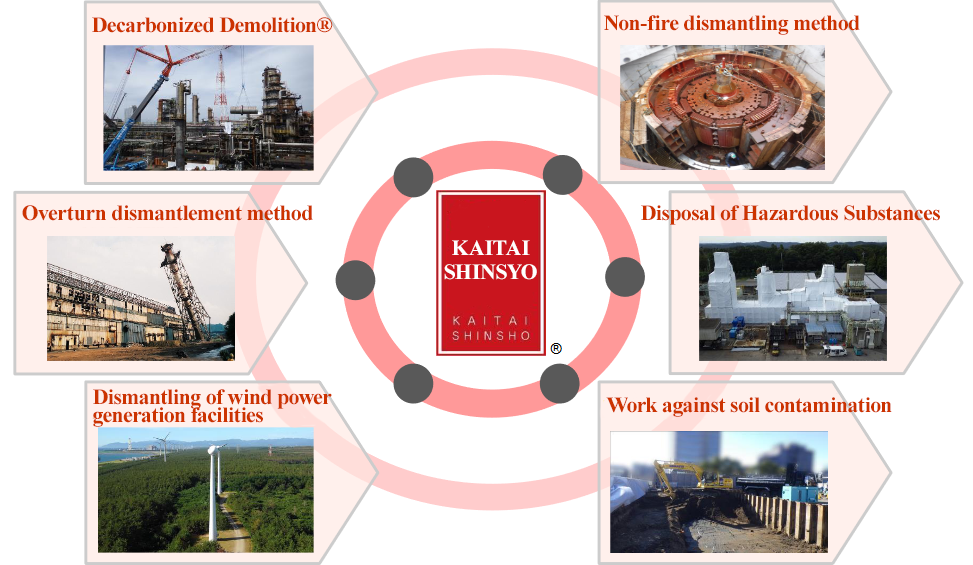
(Source: The company)
(Main decarbonized demolition solutions)
◎ Decarbonized Demolition®
The company offers demolition work that excels in terms of demolition period, cost, and safety and has a highly competitive advantage. The company dismantles various plants using various environmentally friendly demolition methods, such as the apple peeling method, which cuts spirally from the center of the outer shell ceiling like peeling an apple when dismantling spherical storage tanks such as gas holders and oil tanks.
Starting with the apple peeling method and the overturning method, the company holds and is applying for a number of technical patents in regard to buildings and areas the company works on, such as tanks, boilers, chimneys, cranes, 3D, and windmills.
The company will propose dismantling methods using competitive patented methods that achieve safety, cost reduction, shortening of the dismantlement period, and reduction of CO2 emissions, which will lead to practical applications.
◎ Overturn dismantlement method
Steel structures such as chimneys, towers, and tanks have a tipping axis that is the center of gravity fixed by a solid concrete foundation and anchor bolts.
The company's overturning method is a dismantlement method that can reliably control the overturning direction and safely overturn in a predetermined direction by carefully calculating the overturning axis and cutting the concrete foundation.
In addition, it is possible to reduce costs and shorten the demolition period caused by transporting and assembling large cranes. Therefore, it can reduce CO2 emissions up to 1/10 compared to the method of dismantling while lifting with a regular crane.
◎ Dismantling of wind power generation facilities
The amount of wind power generated in the world is 486,790 MW, which is increasing by about 20% every year, and there is a shift to offshore wind power generation, which generates more power.
In Japan, most of them are also land-based, but there is a shift to offshore types. Land-based wind turbines have a useful life of about 15 to 20 years, and the wind turbines for power generation that were installed in the early stage have reached the limit of their use. Furthermore, it is assumed that a considerable number of them need to be dismantled due to damage or fatal failure due to lightning strikes, typhoons, etc.
In such a market environment, the company concluded a licensing agreement with Hitachi Power Solutions Co., Ltd. for the company's patented dismantling method for dismantling domestic onshore wind power generation facilities.
By combing Hitachi Power Solutions Co., Ltd.'s strengths (achievements as a Hitachi Group, abundant technology related to wind power generation equipment, advanced technology for power plant design and maintenance) and the company's strengths (unique demolition methods and know-how, extensive experience in demolition of plants, rich experience in environment-related work), the company has established superiority in terms of shortening the dismantlement period, reducing CO2 emissions, and ensuring safety. The company will strive to capture demand in the wind power generation facility dismantling market.
◎ Fire-free dismantling method
The company's non-fire dismantling method, which does not use fire, captures demand for demolition work in plant premises where the use of fire is limited and dismantling work, such as transformers containing hazardous substances (PCB), and is producing great results.
With the company's unique know-how, it is possible to cut large equipment with a thickness that exceeds the standard in the industry, and it is expected to be used in the decommissioning of nuclear power plants in the future. The company is also developing new cutting blades for this method.
◎ Handling PCB and asbestos
- Stripping of PCB containing films
PCB (polychlorinated biphenyl) is one of the chemically synthesized organochlorine compounds. It is colorless, transparent, chemically stable, heat-resistant, insulating, and non-water-soluble, so it has various applications such as an insulating oil for electrical equipment such as transformers, capacitors, and ballasts, and a solvent for pressure-sensitive paper, paints, and printing inks. However, its production was discontinued in 1972 because it was easily absorbed into the body, highly persistent, and was associated with chronic toxicity, such as skin disorders.
When the Ministry of the Environment investigated the use of PCBs in buildings (chemical plants, oil storage tanks, gas tanks, bridges, etc.), the surveyed facilities were constructed or repainted between 1966 and 1974. Of these, it was estimated that 1%, or about 90 billion yen, requires proper disposal of PCB coatings. Since the survey subject was mainly public structures owned by local governments, the demand for private facilities is expected to increase in the future.
The company has concluded a business alliance agreement with Mitani Sangyo Co., Ltd. for surface coating removal work when dismantling spherical gas holders. The company has established technology for safely removing PCB-containing coatings that are difficult to remove by combining Mitani Sangyo's shot blasting (surface paint stripping) technology with the company's dismantling technology.
- Asbestos removal
Asbestos is a fibrous silicate mineral that is naturally produced, and because its fibers are extremely fine, unless necessary measures are taken when using it in facilities such as grinders and cutting machines, the asbestos will scatter and be inhaled by humans, potentially causing lung cancer and malignant mesothelioma.
Asbestos-related laws and regulations were revised in April 2022, strengthening measures to prevent the scattering of asbestos during the demolition work of buildings.
In anticipation of the expansion of the asbestos removal market, the company made Yazawa Co., Ltd., which has advanced technology for asbestos removal, a group company in December 2021, to conduct asbestos removal work in-house.
◎ Work against soil contamination
Soil pollution means soil being contaminated with hazardous substances (heavy metals, volatile organic compounds, chemicals, oil, etc.). Owners of land with facilities that use hazardous substances that have been abolished, such as factories, are obligated to detoxify soil contamination based on investigations by designated organizations.
The plants to be dismantled by the company cover a large area, and appropriate treatment of soil contamination is required. The company anticipates that there will be many projects for coping with soil contamination associated with the renovation and decommissioning of facilities in the future.
(Main measures/policies)
The company will promote the following measures to expand carbon-free demolition solutions.
◎ Enhancement of bases
In order to acquire recurring revenue-type orders (continuous orders from customers, permanent work on the same premises) and receive more orders nationwide, the company opened an office in Kitakyushu City, Fukuoka Prefecture, which is close to the Kitakyushu factory area. Moreover, the company is expanding its bases in western Japan, including the establishment of a new workshop in Kurashiki City, Okayama Prefecture.
The company is also considering opening offices in Nagoya, Osaka, and Sendai.
◎ Strengthening cooperation with partner companies
The company will build a platform for plant dismantling technology for decommissioning-related business by promoting partnerships with other companies that make the most of each other's strengths.
Main partners
Company | Strengths and Characteristics | Business Partnership |
Hitachi Plant Construction, Ltd. | ・Sales/on-site management/work for nuclear power plants (decommissioning, repair, etc.) ・Demolition work using dismantling technologies such as a large band saw ・Radiation control
| July 2018 |
DAI-ICHI CUTTER KOGYO K.K. | ・Provision of diamond and water jet technology ・High work quality | September 2018 |
REVER HOLDINGS CORPORATION | ・Material recycling (Major Venous) ・Industrial waste treatment | September 2019 |
◎ Increase of orders received as a prime contractor
The company aims to improve profitability by increasing direct orders received and the ratio of projects the company undertake as a prime contractor and public projects. In order to strengthen the system for projects the company undertake as a prime contractor, the company is working on promoting the qualification acquisition system, increasing the number of sales support personnel, and reforming the personnel system.
②Overview of key strategies: DX plant solutions
The group companies, 3D Visual K.K. and Hiro Engineering Co., Ltd., will create new services with their unique know-how and the latest technologies to provide solutions that utilize DX technologies.
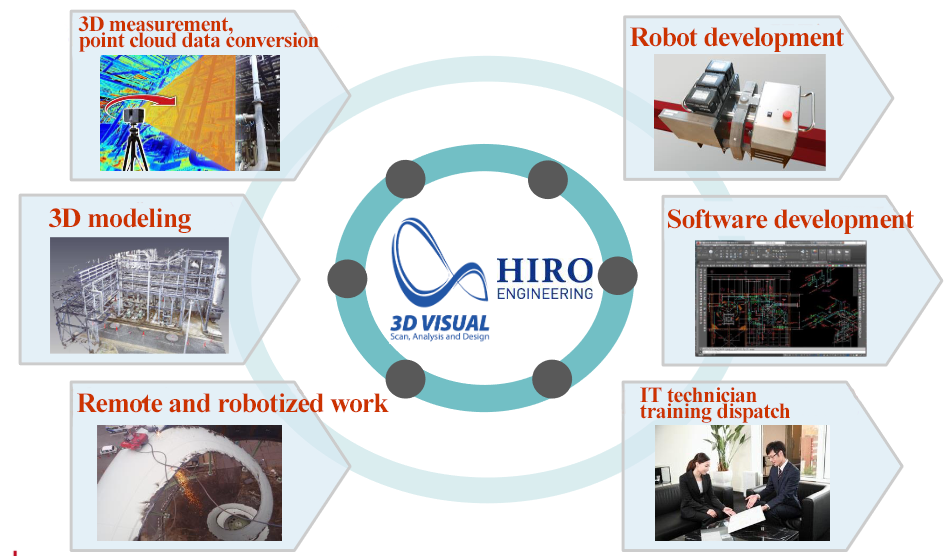
(Source: The company)
(Main Efforts)
◎ 3D measurement and modeling (reform of design and processes)
The company will provide demolition work that "visualizes" the process by converting the paper data at the time of construction more than 30 years ago into the latest 3D data.
◎ Remote and robotized work
Combining the company's unique demolition technology and robot control technology, the company will adopt human-robot collaborative work that can be carried out remotely and robotized at work-sites.
◎ Expand sales of piping and plant design system AUSE/V3
The number of users of AutoCAD provided by AUTODESK® is about 700 million worldwide, and it has built the largest community in CAD software.
3D Visual K.K., a group company, developed AutoCAD add-on software, AUSE, to further improve functions, enhance compatibility, strengthen product appeal, and expand sales through a subscription model.
◎ Crane rail inspection robot (innovation of inspection methods)
Overhead cranes, which are installed in plants and factory facilities and used to transport heavy objects and parts, are subject to distortion due to deterioration over time and, if left unattended, can lead to serious accidents. Therefore, the Safety Regulations for Cranes by the Industrial Safety and Health Act require crane installation companies to conduct self-inspections annually and monthly.
However, conventional visual inspections had challenges, such as the risk of accidents due to workers climbing up the ceiling, unevenness due to visual inspection, and opportunity loss due to the suspension of factory operations during the inspection.
In order to carry out this periodic inspection safely and efficiently, the company has jointly developed with iXs Co. Ltd. a robot that runs on crane rails and performs inspections.
The robot provides crane installation companies with advantages such as less risk of workers getting into accidents, always acquiring accurate and precise data, inspections being done in a short time, and inspections being possible in spare time.
◎ Capital and business alliance with Crassone Co., Ltd.
In September 2022, the company signed a capital and business alliance agreement on demolition DX technology with Crassone Co., Ltd., which operates a platform for demolition work.
By establishing a system where both companies provide their different fields of expertise, such as the company's know-how related to actual work and recycling of waste material processing that it has cultivated over many years in the demolition business and the knowledge of IT and online services that Crassone has accumulated in the matching platform business, Besterra aims to expand the business of both companies through bringing DX to the demolition business, which is expected to increase in the future.
③Overview of key strategies: Personnel strategy
The company will promote HR transformation. The company will transform the corporate culture by increasing employee engagement to trigger further innovation.

(Source: The company)
(Main Efforts)
◎ Improving recruitment
As an investment in the future, the company will actively promote the hiring of construction supervisors. It will also increase the number of recruiters to improve the hiring system, and it will promote diversity by increasing the number of women hired.
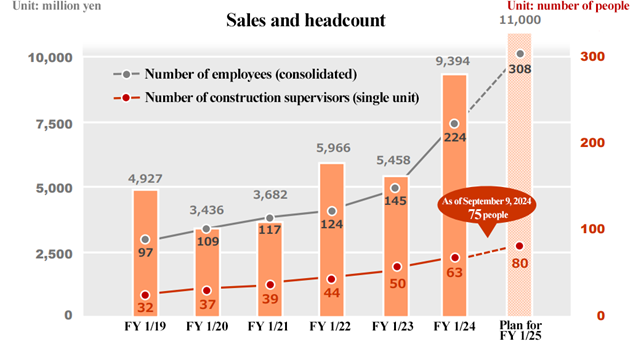
(Source: The company)
◎ Establishment of training programs
The company will establish an advanced demolition engineer training program which is a system for passing on skills from experienced engineers to less experienced engineers.
After training for joining the company and acquiring qualifications in follow-up training, employees will select a course of professional or management positions in mid-career training. After that, the company can foster an entrepreneurial spirit through management training.
The company will formulate and operate a personnel system that focuses on individual work styles.
◎ Knowledge management
The company will transform the tacit knowledge and technology, which are based on the experience and knowledge of individuals unevenly distributed within the company, through the creation of information databases and the use of communication tools, into explicit knowledge shared throughout the organization. By visualizing and efficiently using this explicit knowledge, the company will eliminate information asymmetry and promote organizational growth.
◎ Adoption of a commendation system
The company has adopted a regular commendation system (monthly MVP commendation, etc.) that applies to all employees and recognizes employees who embody the corporate culture and those who have achieved outstanding results monthly and yearly to enhance the corporate culture of praising and appreciating employees who take the initiative.
◎ Establishment of an environment in which employees can work for a long time with peace of mind
The company is making efforts to improve the working environment, by offering the highest level of income insurance in Japan, a retirement allowance system, generous subsidies for employee stock ownership associations (incentives are 15% of the accumulated amount), special paid leave (80 days, which exceeds the maximum number of days allowed under the Labor Standards Act: 40 days).
(4) Investment plan
In order to accelerate the growth speed, the company will actively invest a total of 3.5 billion yen over three years, mainly in DX plant solutions.
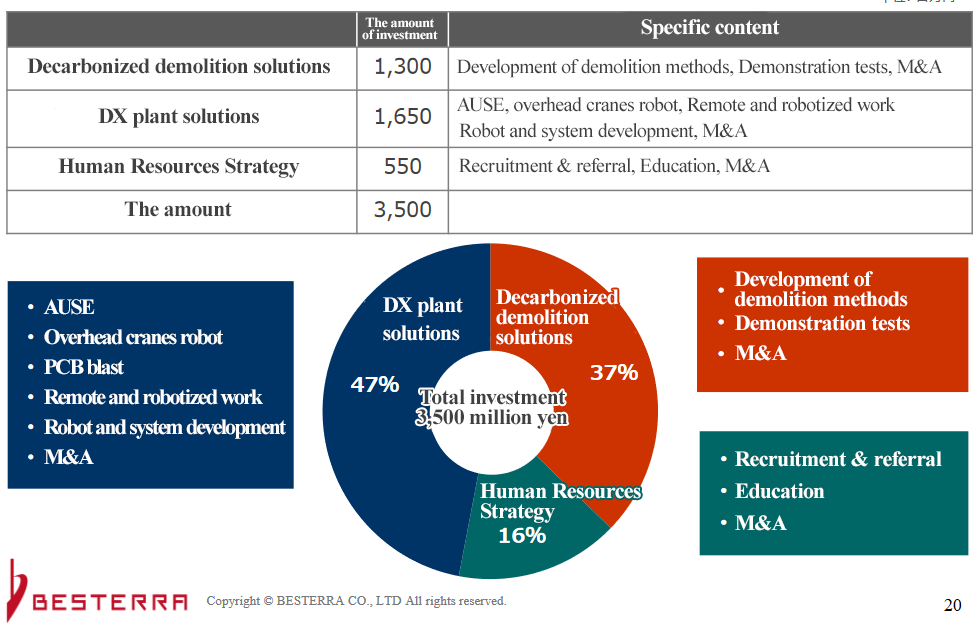
(Source: The company)
(5) Shareholder Returns
The company will pay stable dividends with a target payout ratio of 40%.
In the term ended January 2023, the company changed (expanded) its shareholder benefits and established the "Besterra Premium Benefits Club."
For details of the "Besterra Premium Benefits Club," please refer to the following URL:
https://besterra.premium-yutaiclub.jp/
(6) Long-term vision: Objectives of BESTERRA
Aim to achieve sales of 100 billion yen and profit of 10 billion yen as soon as possible.
5. Conclusions
In the first half of the fiscal year, sales and profit increased significantly, far exceeding the company's forecast disclosed in June. Although the company did not revise its full-year forecasts for sales and operating income at the time of the announcement of the earnings for the first half, it seems that there is considerable room for improvement. In addition, operating income in the second quarter (May-July) was 194 million yen, showing a significant increase from the 17 million yen in the first quarter (February-April). This was due to the decrease in the impact of unprofitable orders and steady progress in demolition projects. In the previous report, we stated that "improving the profit margin is a challenge," and it appears that profit margin has actually improved and is expected to expand in the future as the posting of sales from unprofitable orders declines further. It can be said that the company is entering the stage of full-fledged profit growth. The company appears to be making progress in developing an organizational structure that can withstand significant growth in sales through steady personnel recruitments.
While “decarbonized demolition solutions (innovation through construction methods),” which is the core strategy of the “Action Plan for Decarbonization 2025,” demonstrated strong growth, progress in “DX plant solutions (innovation through IT)” was slow, but the potential demand is large in both areas, with the business environment being favorable.
Under the new management structure, the company will focus on further improving its profit margin while leveraging the company's strengths to develop the market at the expected speed.
<Reference: Regarding Corporate Governance>
◎ Organization type and the composition of directors and auditors
Organization type | Company with an audit and supervisory committee |
Directors | 8 directors, including 5 outside ones |
Auditors | 3 auditors, including 3 outside ones |
◎ Corporate Governance Report Update date: April 25, 2024
Basic policy
In order to promote sound business administration and win social trust sufficiently, our company recognizes corporate governance as the most important issue, puts importance on the improvement of the soundness, transparency, and fairness of business administration, and complies with laws and regulations thoroughly, and all executives operate business while keeping in mind that “the violation of laws or regulations would lead to management responsibility.” In detail, our company disseminates and executes business pursuant to laws, regulations, and in-company rules thoroughly, by developing appropriate systems for making decisions about business administration, fulfilling duties, supervising work, conducting internal control, etc.
It is also important to reform management systems for “achieving appropriate share price” and “increasing share price sustainably” to emphasize shareholders and strengthen the function to check business administration, to establish global-level corporate governance. The results of such efforts would win the trust of society, increase corporate value, and satisfy shareholders.
<Reasons for Non-compliance with the Principles of the Corporate Governance Code (Excerpts)>
【Supplementary Principle 4-1-3】
We do not have a concrete plan regarding the successor of the CEO. As for the Board of Directors, the policy regarding the selection of successors is to take into consideration the personality, insight and accomplishments of each candidate and select a suitable person. In case of formulating and conducting a plan regarding the successor, we shall ensure the fairness, transparency and objectivity of the decision process and appropriately proceed with the selection by involving the Nomination and Compensation Committee, an advisory institution to the Board of Directors where outside directors account for the majority, alongside proactive involvement of the Board of Directors.
【Supplementary Principle 4-3-3】
While we have not clearly established objective, timely and transparent proceedings for the dismissal of the President or CEO, we assess the effectiveness of the Board of Directors every year and shall progress with objective, timely and transparent proceedings through the involvement of the Nomination and Compensation Committee, where outside directors account for the majority, in regard to the nomination and compensation of directors.
<Disclosure Based on the Principles of the Corporate Governance Code (Excerpts)>
【Principle 1-4 Strategically held shares】From the viewpoint of business expansion based on maintaining and strengthening long-term, stable partnerships with business partners, etc., we will acquire and hold the shares of business partners, etc., if we judge that this will contribute to the improvement of our mid/long-term corporate value. For equity investments premised on forming business alliances, the management meets with and receives explanations of the operating environment, business strategy, and purposes of the capital alliance from representatives of the other party. Based on this, the Board of Directors comprehensively evaluates the appropriateness of the stock valuation report and judges whether the deal should take place. For strategically held shares, the Board of Directors constantly checks whether the holding of such shares will contribute to the improvement of our corporate value and confirms the purpose and rationality of said holding based on that check. Our company will appropriately buy/sell shares and exercise voting rights in accordance with relevant regulations, based on a comprehensive evaluation from the viewpoint of improving our corporate value.
【Supplementary Principle 3-1-3 Measures for sustainability】
Our company discloses initiatives concerning sustainability in the mid-term management plan and on our website. Moreover, in order to clarify initiatives for sustainability, we shall set up a Sustainability Committee as an advisory institution of the Board of Directors to control and manage the initiatives in addition to establishing the basic sustainability policy. Furthermore, we view the recruitment and education of human resources as an important challenge for improving our corporate value in the mid- to long-term and we shall create a system which will allow for independent building of career and build a free and lively corporate culture based on diversity to seek the reinforcement of human capital.
As for risks and opportunities for gaining income related to climate changes, we shall respond to the proposal by TCFD in expressing the endorsement of TCFD and participating in TCFD Consortium, and we shall proactively engage in enriching the quality and quantity of disclosures based on TCFD and equivalent frameworks and forge ahead with the enrichment of disclosure on our company website, etc.
【Principle 5-1 Policy on constructive dialogue with shareholders】Regarding requests from shareholders for dialogue (interviews), our company believes that we should express a positive attitude within a reasonable scope in order to contribute to sustainable growth and medium- and long-term improvement of the corporate value of our company. Aiming to promote constructive dialogue with shareholders, with the planning department designated as a department in charge of IR activities, our company holds financial results briefings targeted at financial institutions and investors semiannually and discloses corporate information as needed on our website and through the system of optional disclosure offered by Tokyo Stock Exchange.
【Actions to Achieve Management Conscious of Cost of Capital and Stock Price】
Our company has formulated the "Decarbonization Action Plan 2025," which clearly defines its contribution to a more decarbonized society and defined key strategies and implemented various measures to improve its corporate value over the medium/long term. Our company estimates its current cost of equity to be around 6%. Regarding the balance between cost of capital and return on capital, the average ROE over the past nine years has been 13.2%, and our company considers the equity spread under normal circumstances to be around 7%.
However, regarding the decline in ROE over the past four years, our company recognizes that this is due to a temporary decline in the operating income margin of the plant dismantling business caused by one-time losses from projects that occurred during the management changeover and the acceptance of low-profit projects aimed at stabilizing profits through the expansion of sales scale, as well as the costs associated with actively hiring construction personnel, which is an important factor in scaling up.
In the fiscal year ending January 2026, the final year of the medium-term management plan "Decarbonization Action Plan 2025," our company expects that these temporary factors will disappear, and the scale of operations will exceed fixed costs, leading to an improvement in the earnings structure. As a result, our company anticipates that ROE will exceed 13% and equity spread will exceed the usual 7%.
Based on the current assessment, our company will steadily promote its business in order to achieve sales of 12 billion yen and an operating income of 1.2 billion yen in the fiscal year ending January 2026, the final year of the medium-term management plan "Decarbonization Action Plan 2025." By improving profitability through the expansion of its scale, it aims to achieve an ROE of 13% or higher and further enhance its PBR. At the same time, we will strengthen our efforts in appropriate growth strategies, financial strategies, and other initiatives. For more details, please refer to the disclosed documents regarding our company's measures to achieve management that is mindful of the cost of capital and share price.
This report is not intended for soliciting or promoting investment activities or offering any advice on investment or the like, but for providing information only. The information included in this report was taken from sources considered reliable by our company. Our company will not guarantee the accuracy, integrity, or appropriateness of information or opinions in this report. Our company will not assume any responsibility for expenses, damages or the like arising out of the use of this report or information obtained from this report. All kinds of rights related to this report belong to Investment Bridge Co., Ltd. The contents, etc. of this report may be revised without notice. Please make an investment decision on your own judgment. Copyright(C) Investment Bridge Co., Ltd. All Rights Reserved. |