Bridge Report:(1433)BESTERRA first half of fiscal year January 2020
![]() President Yoshihide Yoshino | BESTERRA CO., LTD (1433) |
![]() |
Company Information
Market | TSE 1st Section |
Industry | Construction business |
President | Yoshihide Yoshino |
HQ Address | Kiba Park Bldg, 3-2-6 Hirano, Koto-ku, Tokyo, Japan |
Year-end | End of January |
Homepage |
Stock Information
Share Price | Share Outstanding (exc. Treasury Stock) | Market Cap. | ROE (Act.) | Trading Unit | |
¥1,233 | 8,226,770 shares | ¥10,144million | 23.8% | 100 shares | |
DPS (Est.) | Dividend Yield (Est.) | EPS (Est.) | PER (Est.) | BPS (Act.) | PBR (Act.) |
¥16.00 | 1.3% | ¥44.61 | 27.6x | ¥317.49 | 3.9x |
*The share price is the closing price on September 9. The number of shares issued was taken from the latest brief financial report. ROE and BPS are the values of the pervious term.
Consolidated Earnings
Fiscal Year | Net Sales | Operating Income | Ordinary Income | Net Income | EPS | DPS |
Jan. 2016 (Actual) | 3,846 | 447 | 464 | 292 | 42.85 | 90.00 |
Jan. 2017 (Actual) | 4,182 | 397 | 404 | 271 | 32.85 | 40.00 |
Jan. 2018 (Actual) | 4,496 | 386 | 373 | 263 | 31.69 | 15.00 |
Jan. 2019 (Actual) | 4,927 | 497 | 495 | 621 | 75.25 | 15.00 |
Jan. 2020 (Forecast) | 5,700 | 525 | 521 | 367 | 44.61 | 16.00 |
* Forecast is from a Company’s financial report. unit: million yen, yen
*From the term ending January 2019, consolidated performance will be posted, and net income means profit attributable to owners of parent (hereinafter called “net income.”)
* Stock split 1:2 in February 2016. 1:3 in February 2017 (EPS has been revised retrospectively)
This Bridge Report reviews on the outlook of BESTERRA’s earnings results for the first half of fiscal year January 2020 and its business plans from fiscal year January 2020.
Table Contents
Key Points
1. Company Overview
2. First Half of Fiscal Year January 2020 Earnings Results
3. Fiscal Year January 2020 Earnings Forecasts
4. Activities for actualizing an advanced recycling society and measures for attaining SDGs
5. Conclusions
<Reference: Regarding Corporate Governance>
Key Points
- For 2Q of the term ending Jan. 2020 (cumulative), sales dropped 9.6% year on year, while operating income grew 9.9% year on year. As the number of completed works declined in 2Q (May to July), sales decreased, but followed the in-company plan. As for profit, gross profit margin improved, because there were many small-scale, profitable works and additional works to the projects to which the percentage-of-completion method is applied. This offset the augmentation of SG&A due to the rise in personnel cost, the rent for the headquarters’ building (the company relocated after selling the headquarters’ building in the previous term), etc.
- There is no revision to the full-year earnings forecast, and it is estimated that sales and operating income will increase 15.7% and 5.5%, respectively, year on year. The backlog of orders as of the end of 2Q fell below that as of the end of the same period of the previous year, but the negotiation for prospective projects is at the final stage. As for profit, the augmentation of personnel and recruitment costs and the cost for investing in R&D and development of a workplace environment (development of a system for allowing employees to work with peace in mind) will be offset. The term-end dividend is to be 10 yen/share, and the annual dividend amount, including the dividend at the end of 2Q, is to be 16 yen/share, up 1 yen/share from the previous term.
- On September 3, the company signed a contract for capital and business tie-ups with REVER Holdings Corporation. REVER Holdings Corporation operates the businesses of recycling metal, home appliances, and automobiles, disposing of industrial waste, etc. via 10 subsidiaries. This is a top-class recycling enterprise in Japan, and has 20 odd footholds mainly in the Kanto region, and in Shizuoka and Osaka, posting annual sales of around 30 billion yen. The company will develop an integrated system for dismantling and recycling under the capital and business tie-ups, to actualize an advanced recycling society and contribute to the earth environment.
1. Company Overview
As a specialist in plant dismantlement, BESTERRA manages the dismantlement of plants (metal structures) for iron-making, power generation, gas, petroleum, etc. Its core competence is “the method and technology for dismantling plants,” and it has many patented methods including international patents. The company concentrates its managerial resources on engineering (proposal, design, and work planning) and management (supervision and work management), and outsources actual dismantlement work to its affiliates, and so it does not own heavy machinery or construction teams (the risk of owning assets can be avoided), and it is unnecessary to procure materials, etc. and make transactions for material production (the inventory risk can be avoided). The corporate name “BESTERRA” was coined by combining the English word “Best (the superlative of ‘good’)” and the Latin word “Terra (the earth),” and、infused with the ambition to “create the best earth.” By developing an integrated system for dismantling and recycling, the company aims to actualize an advanced recycling society and contribute to the earth environment.
Corporate ethos and the code of conduct
Under the corporate ethos “We will contribute to the earth environment with our flexible way of thinking, creativity, and technologies using these concepts,” the company enacted the following code of conduct.
Code of conduct
We will fulfill our responsibilities as professionals.
We constantly develop new technologies, “put a higher priority on safety than anything else,” and offer our services to clients while increasing assurance under the motto “Swifter, more affordable, and safer.”
1-1 Characteristics of the business
The plant dismantlement business accounts for over 97% of total sales (the company also offers staffing services, etc.). The clients for plant dismantlement are leading companies that own plants for ironmaking, electric power, gas, petroleum, etc. In most cases, the equipment installation companies of the corporate groups of clients or leading general contractors are entrusted with dismantlement, and then BESTERRA serves as the primary or second-tier subcontractor. In the term ended January 2019, electric power companies accounted for 35% (22% in the term ended January 2018), steelmakers 41% (37% in the previous term), petroleum/petrochemical companies 9% (27% in the previous term), gas companies 14% (13% in the previous term), and other manufacturers 1% (1% in the previous term).
The company sticks to fabless management, in which it does not own necessary heavy machinery or engineers for dismantlement (so that they can handle any kinds of equipment of plants that have complex structures).
BESTERRA receives valuable materials generated through dismantlement, such as scrap, and sells them to scrap handlers. Accordingly, the company estimates the value of valuable materials while comprehensively considering material, quantity, price (market price of each material, such as iron, stainless steel, and copper), etc. and negotiates with clients about the fee for dismantlement work. In accounting, the gain from sale of valuable materials is included in revenue from dismantlement work, and posted as part of sales from completed dismantlement work. In some cases, contractors (clients) dispose of (sell) scrap, etc. by themselves.
The number of completed works (rough estimates)
| FY 1/18 (non-consolidated) | Ratio to sales | FY 1/19 (consolidated) | Ratio to sales | YOY |
Electric power | 975 | 22% | 1,667 | 35% | +71% |
Steelmaking | 1,639 | 37% | 1,952 | 41% | +19% |
Petroleum/petrochemical | 1,196 | 27% | 429 | 9% | -64% |
Gas | 576 | 13% | 667 | 14% | +16% |
Other | 44 | 1% | 48 | 1% | +9% |
Total | 4,429 | 100% | 4,761 | 100% | +7% |
*unit: million yen
1-2 Strengths: an excellent client base, efficient dismantlement management based on plenty of experience, and intellectual property, such as patented methods
The strengths of the company are excellent client assets, efficient dismantlement management based on plenty of experience, and intellectual property, such as patented methods. Because the clients are basically engineering subsidiary companies of leading companies in ironmaking, electric, gas and coal oil fields, which are easily trustable excellent clients, and it is predicted that they will receive orders continuously. The clients of the leading companies highly evaluate its company’s total management (low cost and high efficiency) of plant dismantlement that it cultivated experiences for 40 years, and it elect a barrier to entry. Furthermore, the company possesses a variety of technologies and know-how, which have been accumulated through environmental work, etc. (14 patents granted and 7 patents pending).
Patented methods, etc.
“Apple peeling demolition method” and fusing robot “Ringo☆Star”
The “apple peeling demolition method” is a method of dismantling a large spherical tank, such as gas holders and oil tanks, by cutting it in spirals from the center of the ceiling of the enclosure part. The cut part spirals down to the ground gradually under the force of the earth’s gravity (natural energy). The method enjoys superiority in a work period, cost, and safety, and has considerable competitive advantages, realizing “greater promptness, higher cost efficiency, and added safety.” Furthermore, the company offers a robot for the fusing process, “Ring☆Star,” which automates the “apple peeling demolition method.”(The company is also working to expand the range of applications for “Ringo☆Star” by developing a new attachment).
Environment-related methods
The company has cultivated experiences and business results of a multitude of environment-related demolition works, using the “fireless methods” which do not require the use of fire. For example, although polychlorinated biphenyls (PCBs) are considered as a toxic substance and therefore totally abolished today, it had been used for many years in transformers and condensers because of its excellent thermal stability and chemical stability (electric insulation characteristics). In many cases, transformers and condensers are disposed of in conjunction with plant demolition works; however, because PCBs gasify when they are treated at the high temperature, posing a risk of inhaling the gas so generated, any firearms (such as gas cutting machines) cannot be used in demolition and withdrawal involving PCBs. The company is skillful at fireless and quasi-fireless methods using saber saws (which cut off objects with their saw blades moving in a reciprocating manner) that can cut off objects thicker than the thickness, which, in the industry, had been considered impossible to cut, through numerous devices, including measures against seizure of motors and recycling of blades. BESTERRA has applied for joint patents with Hitachi Plant Construction, Ltd. for a transformer dismantling method, a transformer dismantling jig, and a cutting device for dismantling a transformer.
Windmill demolition works
The number of power-generating wind turbines continues to increase by about 20% annually worldwide, but the demand for dismantling is expected to increase in the future due to wear and tear and economic obsolescence.According to the material presented by the company, the wind power generation volume worldwide is 486,790 MW (by about 340,000 onshore power generation plants and about 4,000 offshore ones) with an annual growth rate of about 20%. In Japan, the number of wind power generation plants stood at 2,225 as of the end of 2017, expanding by about 90 every year. Meanwhile, as the useful life is approximately 15 to 20 years, and the windmills for power generation established in the early stage are reaching the application limit. Moreover, not a few plants need to be dismantled due to damage or fatal failure caused by thunderbolts or typhoons.
How to knock down a power-generating wind turbine (international patent application)
As some windmills have been built in mountain districts and on the sea, demolition of them is highly difficult. The company has devised a method for dismantling wind turbines that does not require scaffolds, and has already acquired a domestic patent for “Method of knocking down a power-generating wind turbine.” International patents are pending for “Method of knocking down towering structures using their bases” and “Method for dismantling tower-shaped equipment for wind power generation.” Safety of workers can be improved dramatically and the work period can be shortened by using these patent-based methods.
Pursuit of the value of the 3D business
Using services such as layout simulation, strain/bending/torsion measurement, comparison of structures before and after improvement, and video walkthroughs, the company converts physical data taken when plants were established (more than 30 years ago) into the latest 3D data, and uses that to provide detailed information about the dismantling process. They also provide unique 3D measurement services for dismantling work using the latest measuring technology and simulation systems that are capable of drawing data as 2D diagrams, handling BIM/CIM modeling, Perfect 3D, and 3D printing.
“Visualize” the dismantling process
Layout simulation | The equipment models produced with 3D CAD are placed in 3D data, and the replacement of equipment can be simulated. By moving the equipment models, it is possible to check how they interfere and collide with one another. |
Strain, bending, and torsion measurements | It is possible to measure changes in shapes. This is useful for diagnosing frameworks tentatively, to check whether a building got distorted due to an earthquake, deterioration, etc. |
Comparison of structures before and after installation
| The shapes of equipment that changes due to heat and vibration, such as pipes, conveyors, and furnaces, at the time of installation and after operation are compared. With 3D data, it is possible to grasp overall changes intuitively. |
Video walkthroughs
| Walk-through videos are produced by using synthesized point cloud data. These videos can be utilized for presentations and publicity videos regarding dismantlement plans and real estate information. |
Unique 3D measurement service
Draws a two-dimensional diagram | The 3D CAD models based on point cloud data are converted into drawings. It is also possible to produce drawings directly from point cloud data in a simple manner. |
Handles BIM/CIM modeling | Modeling is conducted with 3D CAD based on point cloud data. It is possible to produce models of the parts that require construction or renovation as BIM (building information modeling) data. |
Perfect 3D | This is a large-scale 3D data measurement service combining automobile-based MMS (mobile mapping system), airborne laser measurement, water area measurement, etc. |
3D printing | After modeling with point cloud data, data are processed and deformed so that they can be shaped with a 3D printer. It can produce fine structures with a lamination pitch of 15 μm. |
*Two standards for posting revenue and seasonality of revenue posting of the company
The standards for posting revenue from contracts can be classified into the completed contract method, in which revenue is posted when works are completed, and the percentage-of-completion method, in which revenue is posted according to the progress of works. In the case of plant dismantlement, where valuables, such as scrap, are collected, revenue cannot be confirmed until the sale of scrap. Therefore, the company basically applies the percentage-of-completion method to large-scale projects whose contract amount exceeds 50 million yen and whose period exceeds 3 months (from the term ended Jan. 2018), and uses the completed contract method for other works. The timing of posting revenue from works for which the completed contract method is used is often affected by the equipment investment plans of clients. In the case of Besterra, revenue tends to be posted in the first quarter (Feb. to Apr.) and the fourth quarter (Nov. to Jan.) (the seasonality of revenue posting). However, the variation in quarterly performance may mislead investors, so the company is expanding the scope of application of the percentage-of-completion method step by step, to equalize the timings of revenue posting.
1-3 Medium-term management plan 2021 (from the term ending Jan. 2020 to the term ending Jan. 2022)
Numerical goals
| FY 1/20 | FY 1/21 | FY 1/22 |
Sales | 5,700 | 6,400 | 7,200 |
Operating income (Rate) | 525(9.2%) | 570(8.9%) | 650(9.0%) |
Ordinary income | 521 | 566 | 645 |
Net income | 367 | 403 | 457 |
*unit: million yen
BESTERRA’s medium-term management plan uses a rolling system, in which the plan is reviewed and revised every term in order to deal flexibly with changes in the business environment. The basic strategy of the 2021 medium-term management plan (which began in the term ending January 2020) is to restructure earning and human resources systems, pursue the value of the 3D business, and consider M&As as basic strategies. The company aims to achieve sales and profit growth of 10% or greater, with sales of 7.2 billion yen and an operating income of 650 million yen in the term ending January 2022.
Approaches in the term ending Jan. 2020―the profit structure reform, personnel structure reform, pursuit of 3D business values, M&A strategies
Profit structure reform
As the profit structure reform, the company will expand the number of orders and its business scale, enrich dismantlement methods, and enhance its marketing capability.
Increase in the number and scale of projects for which the company receives orders
Companies with heavy industrial plants are the backbone of the Japanese industry. BESTERRA proposes safe and innovative dismantling work to these companies, aiming to maximize the plant dismantling business. Specifically, individual targets and strategies will be set for the fields of “electric power,” “steel,” “petroleum and petrochemicals,” and “gas and others.”
| Equipment to be dismantled | Strategy | Sales (composition ratio) | |
FY 1/19 | FY 1/22 | |||
Electric power | Boilers, chimneys, tanks, transformers (PCB) | To make transactions for dismantling thermal power stations, equipment including PCB, wind power stations, and for nuclear power plants | 1,659 million yen (35%) | 2.4 billion yen (33%) |
Steel | Blast furnaces, chimneys, reclaimers (machinery) | To cement the relationships with existing clients (blast furnace enterprises) and find new clients (electric furnace enterprises) | 1,928 million yen (41%) | 2 billion yen (28%) |
Petroleum/ petrochemistry | Refineries and ethylene plants | To make transactions for dismantling refineries and ethylene complexes | 425 million yen ( 9%) | 1.9 billion yen (26%) |
| ||||
Gas and others | Gas holders, various manufacturing plants | To improve the promotion of the apple peeling demotion method, and make transactions for factories | 747 million yen (15%) | 900 million yen (13%) |
For enriching dismantlement methods, the company will propose competitive patented demolition methods, such as the cost-competitive “apple peeling demolition method” and “Ringo☆Star” (dismantlement of tanks), the original fireless demolition method (electric power equipment, such as transformers), and the method for dismantling windmills for power generation (wind power generation), whose international patent is pending, and put them into practical use.
As for the improvement of sales force, the company will increase the ratio of demolition works ordered based on prime contracts and enrich sales bases. Currently, the ratio of works as a primary subcontractor entrusted by prime contractors is high. It, therefore, will increase the number of orders received directly from customers and the proportion of prime contract-based works, with the aim of improving earnings ratio. Specifically, the company will enrich advertising media, such as the website, promotional materials, and other various media, as well as present its products and services at exhibitions. BESTERRA is also considering opening new bases.
The company’s current bases and their respective sales as of the end of the term ended January 2019 are: Tokyo Headquarters (3,561 million yen in FY January 2018 → 3,590 million yen in FY January 2019); JFE Chiba factory office (Chiba City, Chiba Prefecture, 550 million yen → 461 million yen); Chiba Office (Ichihara City, Chiba Prefecture, 221 million yen → 271 million yen); West Japan Office (Fukuyama City, Hiroshima Prefecture, 164 million yen → 257 million yen). Currently, the company is planning to expand their West Japan office, and is preparing to open a Keihin office (the company had 180 million yen in sales in the Keihin area in the January 2019 term). They are also considering opening an office in Sendai. The establishment of new bases will lead to an increase of orders for projects with recurring revenue (continuous orders from customer groups, being stationed at factories, etc.).
2. First Half of Fiscal Year January 2020 Earnings Results
2-1 Consolidated results
| 1H of FY 1/19 (consolidated) | Ratio to sales | 1H of FY 1/20 (consolidated) | Ratio to sales | YOY |
Sales | 2,110 | 100.0% | 1,907 | 100.0% | -9.6% |
Gross profit | 392 | 18.6% | 434 | 22.8% | +10.7% |
SG&A expenses | 252 | 12.0% | 280 | 14.7% | +11.1% |
Operating income | 139 | 6.6% | 153 | 8.1% | +9.9% |
Ordinary income | 139 | 6.6% | 153 | 8.0% | +10.0% |
Net income | 90 | 4.3% | 101 | 5.3% | +11.3% |
*unit: million yen
Sales dropped 9.6% year on year, while operating income grew 9.9% year on year.
Sales were 1,907 million yen, down 9.6% year on year. Due to the recoil from the sales growth with large-scale works in the same period of the previous year, sales dropped year on year, but followed the in-company plan (the forecast for the cumulative second quarter has not been disclosed). The sales from the dismantlement of steelmaking plants increased thanks to the contribution of West Japan Office (Fukuyama City, Hiroshima Prefecture), which was upgraded, and Keihin Office (Kawasaki City, Kanagawa Prefecture), which was newly opened. In addition, the sales in the petroleum/petrochemical industry, which were sluggish in the same period of the previous year, increased significantly.
Operating income was 153 million yen, up 9.9% year on year. As there were many small-scale, profitable works and additional works to the projects to which the percentage-of-completion method is applied (before signing a contract for additional works, the works were conducted to meet on-site requests, and costs at that time were posted), cost ratio improved by 4.2 points, and gross profit increased 10.7% year on year, despite the drop in sales. It offset the augmentation of SG&A due to the increase in personnel costs, including the rise in basic salaries (increase in average salaries) and the payment of qualification allowances, the posting of the rent for the headquarters’ building (The company sold its own building, and started renting), the upgrade of the attendance management system for reforming ways of working, etc.
The number of completed works by sector (rough estimates)
| 1H of FY 1/19 (consolidated) | Ratio to sales | 1H of FY 1/20 (consolidated) | Ratio to sales | Increase/Decrease |
Electric power | 590 | 29% | 325 | 18% | -45% |
Steelmaking | 956 | 47% | 1,011 | 56% | +6% |
Petroleum/petrochemical | 102 | 5% | 289 | 16% | +183% |
Gas | 346 | 17% | 144 | 8% | -58% |
Other | 41 | 2% | 36 | 2% | -12% |
Total | 2,035 | 100% | 1,804 | 100% | -11% |
*unit: million yen
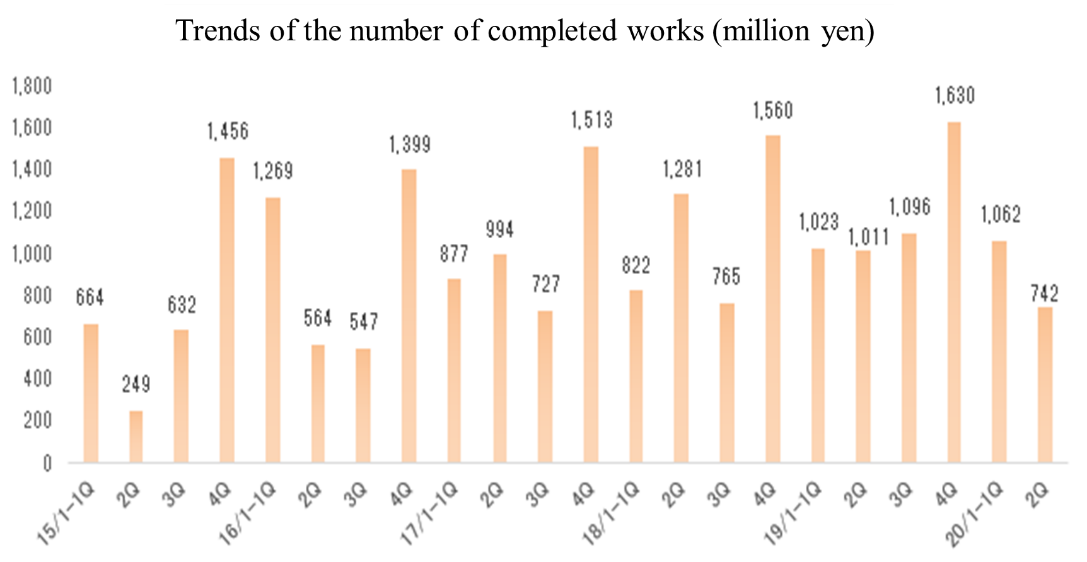
Breakdown of SG&A and major change factors
| 1H of FY 1/19 (consolidated) | Ratio to sales | 1H of FY 1/20 (consolidated) | Ratio to sales | YOY | Major change factors |
Salaries and allowances | 119 | 5.6% | 132 | 6.9% | +11.0% | The increase of salaries for employees |
R&D cost | 9 | 0.4% | 12 | 0.6% | +22.5% | Development of inspecting crane Robots |
Commissions and remunerations paid | 25 | 1.2% | 27 | 1.4% | +7.4% | The upgrade of basic system |
Recruitment cost | 5 | 0.2% | 8 | 0.4% | +61.9% | Advertising media, referral fee |
Advertisement | 15 | 0.7% | 7 | 0.4% | -47.4% | Decrease of exhibition(twice→once) |
Other | 77 | 3.6% | 92 | 4.8% | +19.1% | Leasing expense of head office building |
Total SG&A expenses | 252 | 11.9% | 280 | 14.7% | +11.1% |
|
*unit: million yen
2-2 Progress of plans for human resources
The number of supervisors for dismantlement as of the end of the second quarter was 34 (32 as of the end of the previous term), as two sales staff members became supervisors. In the cumulative second quarter, the number of supervisors increased by only 2, but the number of job interviews is growing, and the company aims to recruit 15 more supervisors from the end of the previous term, to have 47 supervisors at the end of this term. For enhancing the capability of recruitment, the company increased basic salaries and improved a working environment where employees can work with peace in mind in the cumulative second quarter.
Increase of salaries for employees | The company increased basic pay in order to increase the satisfaction level of employees and secure excellent personnel, and adopted a qualification allowance in order to secure qualified workers, who are indispensable for increasing direct orders for dismantlement works.
・Significant increase in basic pay, in addition to a periodic pay rise and personnel evaluation ・Payment of a monthly qualification allowance to supervisory engineers ・The average annual income of employees increased from 5.03 million yen to 5.69 million yen. |
Income insurance | As part of efforts of personnel structure reform, the company adopted “GLTD,” a group income insurance for long-term disabilities, in order to develop an environment where employees can work with peace in mind for a long period of time. “GLTD” means a system for compensating for a certain percentage of the lost income if an employee becomes unable to work for a medium or long period of time due to disease, injury, or mental illness, until the retirement age at the longest, no matter whether said employee is employed or has resigned.
・50% of monthly pay will be covered (the highest in Japan). ・Lost income will be compensated for until the retirement age (60 years old) at the longest, no matter whether the insured is employed or has resigned. ・Insurance premiums will be paid fully by the company. |

2-3 The backlog of orders
| 1H of FY 1/19 (consolidated) | 1H of FY 1/20 (consolidated) | YOY |
The backlog of orders at the beginning of the term | 2,218 | 1,021 | -53.9% |
The amount of works received | 1,163 | 1,615 | +38.9% |
The amount of completed works | 2,035 | 1,804 | -11.3% |
The backlog of orders at the end of the term | 1,346 | 832 | -38.2% |
*unit: million yen
The company concentrates on the receipt of orders for recurring-revenue projects rather than one-shot revenue ones. Namely, the company prioritizes continuous small tasks over one-shot large-scale works. There are many inquiries about dismantlement works, but there are many projects whose period from the receipt of orders to the start/completion of works is short, and the company has not received official orders at the end of the second quarter. Accordingly, the backlog of orders decreased from the end of the same period of the previous year and also from the beginning of this term.
The backlog of orders by sector
| 1H of FY 1/19 (consolidated) | Ratio | 1H of FY 1/20 (consolidated) | Ratio | Increase/Decrease |
Electric power | 487 | 29% | 25 | 3% | -95% |
Steelmaking | 957 | 57% | 532 | 64% | -44% |
Petroleum/petrochemical | 101 | 6% | 183 | 22% | +82% |
Gas | 118 | 7% | 50 | 6% | -58% |
Other | 17 | 1% | 42 | 5% | +148% |
Total | 1,679 | 100% | 832 | 100% | -50% |
*unit: million yen
2-4 Financial condition and cash flow(CF)
Financial condition
| Jan. 19 | Jul. 19 |
| Jan. 19 | Jul. 19 |
Cash | 2,032 | 1,278 | Payables | 1,357 | 384 |
Receivables | 1,785 | 1,173 | Taxes Payable | 250 | 10 |
Current Assets | 4,059 | 2,771 | Borrowings | 7 | 6 |
Tangible Assets | 265 | 277 | Liabilities | 1,949 | 605 |
Investments, Others | 212 | 164 | Net Assets | 2,614 | 2,631 |
Noncurrent Assets | 504 | 466 | Total Liabilities, Net Assets | 4,564 | 3,237 |
*unit: million yen
The total assets as of the end of the second quarter stood at 3,237 million yen, down 1,327 million yen from the end of the previous term. The collection of accounts receivable progressed, but cash and deposits decreased, due to the repayment of accounts payable and the payment of income tax, dividends, etc. In addition, noncurrent assets declined due to the change in the accounting standards (tax effect accounting). Capital adequacy ratio was 81.2% (57.2% at the end of the previous term).
Cash Flow(CF)
| 1H of FY 1/19 (consolidated) | 1H of FY 1/20 (consolidated) | YOY | |
Operating Cash Flow | 153 | -539 | -692 | - |
Investing Cash Flow | -12 | -132 | -120 | - |
Financing Cash Flow | -234 | -81 | +152 | - |
Cash and Equivalents at Term End | 663 | 1,277 | +614 | +92.7% |
*unit: million yen
Operating CF was an expenditure of 539 million yen, as quarterly net profit before taxes and other adjustments was 153 million yen (139 million yen in the same period of the previous year), depreciation was 16 million yen (15 million yen in the same period of the previous year), accounts payable decreased 973 million yen (it decreased 130 million yen in the same period of the previous year), and the company paid 236 million yen for income tax, etc. (17 million yen in the same period of the previous year).
2-4 Collaborative development of a robot for inspecting crane rails with iXs Co., Ltd.
In collaboration with iXs Co., Ltd. (Kawasaki City, Kanagawa Prefecture; representative directors: Fuminori Yamasaki and Takashi Karino), the company developed a self-propelled inspection robot, which would contribute to the safe, efficient periodic inspection of overhead cranes (used for carrying heavy objects and parts, etc.) set at plants, factory equipment, etc.
Current inspections of overhead cranes whose efficiency and safety need to be improved
Overhead cranes get distorted due to deterioration, etc., and if it is untreated, a serious accident may occur. Accordingly, enterprises that have installed cranes are obligated to conduct an annual voluntary inspection, which is conducted by applying a load onto each crane, and a monthly voluntary inspection, which is carried out for specific items, in accordance with the provisions regarding safety of cranes, etc. in the Industrial Safety and Health Act. However, the current inspections are mainly the measurement and visual inspection by educated workers, and it is necessary to suspend the entire operation of factories for several days for the inspections. In addition, workers need to climb onto overhead cranes for the inspections, so the securing of safety for these workers is an issue to be solved, and some effective measures for improving efficiency and safety are demanded.
Characteristics of the developed self-propelled inspection robot
When the developed self-propelled inspection robot runs on a crane rail, it can obtain the three-dimensional displacement data of the crane rail, including span length, rail gradient, and the horizontal difference between right and left rails. In other words, it is possible to conduct three-dimensional position measurement under an unmanned, high-load environment, and this would solve the problems with efficiency and safety. In addition, it can accurately inspect the mismatches and gaps of rail joints, small cracks, etc., which are difficult to check with conventional inspection systems. By obtaining images and point clouds in addition to coordinate values, it is possible to inspect the shapes and surfaces of the entire girders, and generate added value in addition to rail measurement.
Business model
As an advanced 3D measurement service, the company conducts measurement using a self-propelled inspection robot, and iXs Co., Ltd. analyzes obtained data. At present, about 100,000 cranes are in operation in Japan, and an annual voluntary inspection costs about 300,000 yen. Accordingly, the company estimated that the mandatory inspection market has a scale of over 30 billion yen. Since many existing clients for the dismantlement business use this service, the company can utilize the existing sales channels. The company plans to start accepting orders in the term ending January 2022. While contributing to the safety control and equipment management for plants, factory equipment, etc., the company hopes to utilize its knowledge for preventive maintenance and deterioration prediction in the future.
What is iXs Co., Ltd.?
Under the mission to “protect society with robots and technologies” and the concept of “usability” and “durability,” iXs Co., Ltd. develops inspection robots for social and industrial infrastructures and robots for special environments, and analyzes obtained data. iXs keeps offering high added value by saving labor and increasing safety with robots, to tackle social issues in Japan, such as the rapidly progressing deterioration of infrastructure and the shortage of veteran engineers.
Inspection robot whose design registration is pending (conceptual diagram) | |
![]() |
|
(Source: Company’s material)
3. Fiscal Year January 2020 Earnings Forecasts
Consolidated Earnings
| FY 1/19 | Ratio to sales | FY 1/20 (forecast) | Ratio to sales | YOY |
Sales | 4,927 | 100.0% | 5,700 | 100.0% | +15.7% |
Operating income | 497 | 10.1% | 525 | 9.2% | +5.5% |
Ordinary income | 495 | 10.0% | 521 | 9.1% | +5.2% |
Net income | 621 | 12.6% | 367 | 6.4% | -41.0% |
*unit: million yen
Considering prospective projects, the company has not revised the full-year earnings forecast. It is estimated that sales and operating income will grow 15.7% and 5.5%, respectively, year on year.
As the backlog of orders as of the end of the second quarter was 832 million yen, down 38.2% from the end of the same period of the previous year, the company needs to post sales of 3,792 million yen (up 34.7% year on year) in the second half, in order to reach the estimated annual sales, but it seems that the negotiation for prospective projects is progressing healthily.
As for profit, the company took into account the augmentation of costs for recruitment and personnel, and also the costs for investment for growth, including R&D of new dismantlement methods, recruitment activities, the improvement of the working environment (to enable workers to work with peace in mind), and the installation of systems for efficient task management. Net income is projected to decline, because the extraordinary income from the sale of the headquarters’ building was posted in the previous term.
The progress rates toward full-year estimates are 33.5% for sales (the progress rate toward the actual annual sales in the previous yea 42.8%), 29.3% for operating income (28.1% in the previous year), 29.4% for ordinary income (28.1% in the previous year), and 27.5% for net income (14.6% in the previous year). The amount of completed works of the company is seasonal according to the equipment investment plans of clients. Accordingly, the sales of the company tend to be posted in the fourth quarter (Nov. to Jan.).
The term-end dividend is to be 10 yen/share, and the annual dividend amount, including the dividend of 6 yen/share at the end of 2Q (up 1 yen/share), is to be 16 yen/share, up 1 yen/share from the previous term. (The estimated payout rati 35.9%) The company plans to pay dividends stably with the aim of achieving a payout ratio of 40%.
3-2 Capital and business tie-ups with REVER Holdings Corporation
On September 3, the company concluded a contract for capital and business tie-ups with REVER Holdings Corporation (headquartered in Chiyoda-ku, Tokyo; representative director and president: Naoto Matsuoka), and received 2.5 million shares of REVER Holdings (accounting for 14.59% of the total number of outstanding shares) from INCJ, Ltd. (Chiyoda-ku, Tokyo; representative director and president: Mikihide Katsumata).
Outline of REVER Holdings Corporation
REVER Holdings Corporation is a holding company that operates the businesses of recycling metal, home appliances, and automobiles, disposing of industrial waste, etc. via 10 subsidiaries. Its corporate group has 20 odd footholds mainly in the Kanto region, and in Shizuoka and Osaka. It has a history of over 110 years. REVER Holdings is a leading material recycler in Japan, and has been pursuing the economies of scale through active M&A in the field filled with small and medium-sized enterprises, with the aim of becoming a Japanese giant material recycling company. REVER Holdings aims to take a role in the recycling society by promoting the “recycling business,” which accepts and recycles waste discharged from society, and offering a one-stop service of disposing of and recycling waste nationwide.
INCJ, Ltd. is a 100% subsidiary of Japan Investment Corporation. This company offers funds for growth to enterprises possessing innovativeness for creating new added value by utilizing “open innovations” beyond industrial and organizational borders, and supports them while getting involved in business administration.
Group companies of the REVER Holdings
Suzutoku Ltd. (Chiyoda-ku, Tokyo; recycling and disposal of waste, mainly metal), Metal Recycling Co., Ltd. (Kawajima-machi, Hiki-gun, Saitama Prefecture; recycling of mainly automobiles, disposal of wastes, and sale of used auto parts), Nakadaya Corp. (Chiyoda-ku, Tokyo; recycling of industrial waste, including ferrous and non-ferrous metal and office automation devices), Sunny Metal Corp. (Konohana-ku, Osaka-shi, Osaka; recycling of mainly metal, disposal of waste, and recycling of home appliances), Phoenix Metal Corp. (Ichihara-shi, Chiba Prefecture; recycling of a variety of items, including ferrous and non-ferrous metal, industrial waste, and home appliances), NNY Corp. (Otawara-shi, Tochigi Prefecture; recycling of mainly non-ferrous metal and disposal of waste), Itsumo Corp. (Chiba-shi, Chiba Prefecture; transportation of resources, waste, etc.), Shinsei Co., Ltd. (Namegawa-machi, Hiki-gun, Saitama Prefecture; intermediate processing, collection, and transportation of waste), Major Venous Japan Co., Ltd. (Chiyoda-ku, Tokyo; processing, treatment, and recycling of waste, etc. and support for waste management), HIDAKA SUZUTOKU (Thailand) Co., Ltd. (Thailand; disposal of factory waste mainly from production sites of Japanese companies).
Purposes of capital and business tie-ups: for the creation of an environmental supply chain (a platform in the venous industry)
The Japanese venous industry has been fragmented and filled with small and medium-sized enterprises, and they think that “the shift to the scale business would improve the advantage of the industry itself and contribute to the actualization of an advanced recycling society.” Through the capital and business tie-ups, the company will create an environmental supply chain (a platform in the venous industry), and call on small-sized enterprises to join the platform, with the aim of becoming a major company in the Japanese venous industry.
Current situation of and problems with the venous industry
While the manufacturing industry or the like, which produces products, is called an arterial industry, an industry that collects, treats, recycles, and reuses waste and used products in dismantlement works, etc. is called a venous industry, likening it to blood circulation. The venous industry, which recycles waste, is indispensable for actualizing a recycling society, but the Japanese venous market is filled with small and medium-sized enterprises and is suffering cutthroat competition. The cooperation between the arterial and venous sectors has not been achieved, so it is difficult to form a recycling system. Compared with European and U.S. enterprises, which are getting larger, the enterprises in the Japanese venous industry lack competitiveness.
They aim to establish a position as a contact point between the arterial industry and the venous industry.
While Besterra Co., Ltd. mainly operates the dismantlement business, which is positioned between the arterial industry (including electric power, steelmaking, and petrochemistry) and the venous industry (including scrap and industrial waste), REVER Holdings Corporation mainly conducts the intermediate processing of scrap, industrial waste, etc. in the venous industry.
As the market is expected to grow due to the implementation of measures for coping with the deterioration of social infrastructure, etc., they will take a role of connecting the arterial and venous industries, and aim to establish an indispensable position in the advanced recycling society by joining hands in the medium to long term.
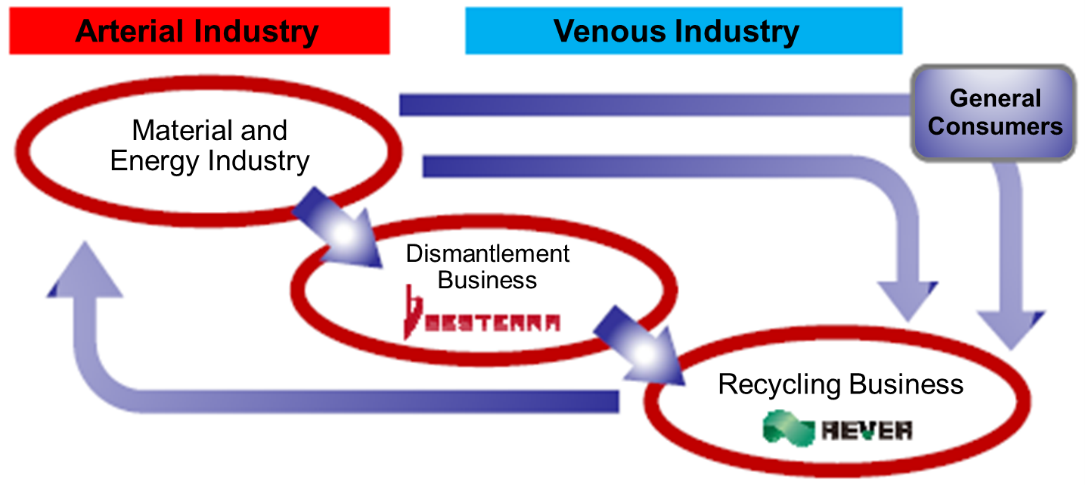
(Source: Company’ material)
Effects of alliance
・ Improvement in the capability of giving proposals to client companies and sharing of information on client companies
They will conduct proposal-based promotion of their one-stop service based on the plant dismantlement technology of Besterra and the recycling technology of REVER Holdings. Especially, they hope to receive more orders for projects for improving environment-friendliness. The dismantlement works of Besterra are ordered mostly by companies in Japanese key industries, which have deteriorated facilities, and there is growing demand for environmentally friendly management.
・ Enhancement of influence (economies of scale) through the pursuit of business scale
By taking a role of connecting the arterial and venous industries, the company will establish its position as an indispensable enterprise or platform in an advanced recycling society. This would certainly boost the capability of giving proposals to client companies and lead to the sharing of information. In parallel, the company will pursue economies of scale, strengthen its ability to negotiate about prices, and increase opportunities to receive orders.
Acquired 14.59% of outstanding shares
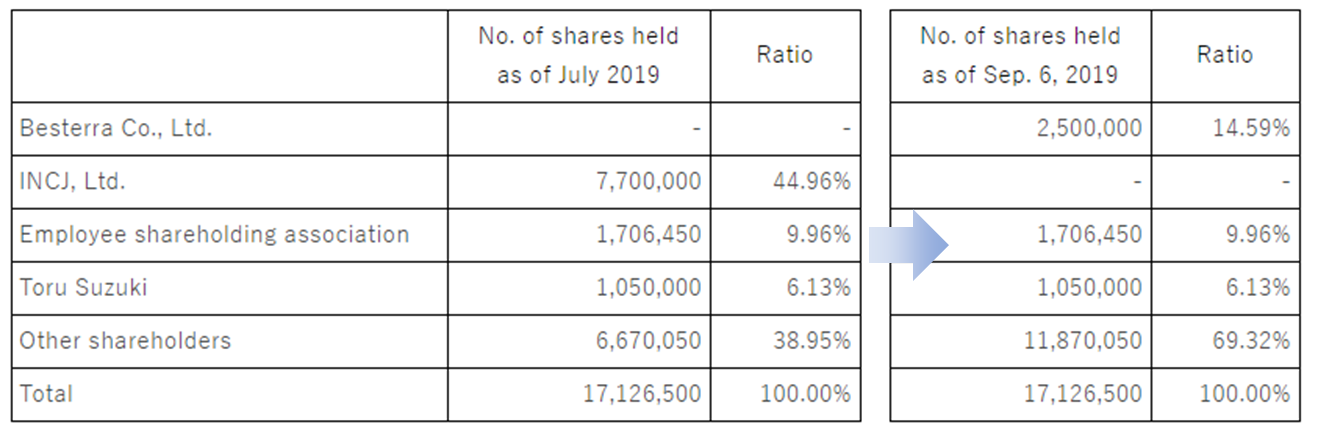
*Other shareholders include Tokyo Tekko Co., Ltd. (513,800 shares) and IBOKIN Corp. (205,000 shares).
The company plans to prepare funds for acquiring the shares by using cash on hand and borrowing. It thought of procuring funds via direct financing, but considering the current capital composition, it judged that it is appropriate to procure funds via indirect financing.
4. Activities for actualizing an advanced recycling society and measures for attaining SDGs
With the aim of realizing BEST (the best) TERRA (the earth), which is the origin of the corporate name, the company will contribute to the attainment of the sustainable development goals (SDGs) with its plant dismantlement business. In addition, the company will share and implement managerial policies with REVER Holdings Corporation, which aims to become a major company in the venous industry, to actualize sustainable business operation and expand the businesses of both companies.
4-1 Roles and activities of the company for actualizing an advanced recycling society
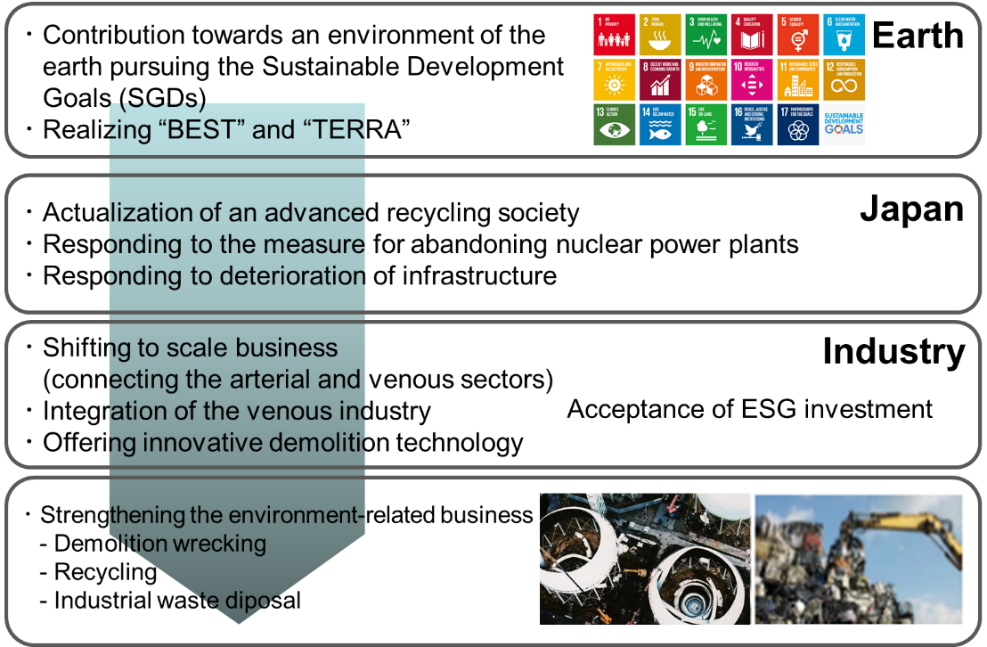
(Source: Company’s material)
At a global level, the company aims to actualize BEST (the best) TERRA (the earth), which is the corporate name, by contributing to the earth environment by making efforts to attain sustainable development goals (SDGs). The capital and business tie-ups with REVER Holdings Corporation is part of this activity. In Japan, the company will work on the response to the measures for abandoning nuclear power plants and measures for coping with the deterioration of infrastructure, in addition to the actualization of an advanced recycling society. Then, as a leader in the plant dismantlement field, the company will lead the restructuring and integration of the venous industry by shifting to the scale business (connecting the arterial and venous sectors), and offer innovative demolition technologies.
For the cooperation with the venous sector, the company will actualize and strengthen an integrated environment-related business by combining the demolition/wrecking business, the recycling business, and the industrial waste disposal business.
4-2 Besterra’s response to SDGs
![]() |
|
(Source: Company’s material)
To develop a workplace environment where worthwhile jobs are offered.
① | The company aims to become a company in which every employee can feel his/her job is worthwhile and proud of his/her future. |
② | The company respects diversity, and strives to enrich the working environment, including social security. |
③ | The company develops an equal educational environment so that workers can exert their abilities to the fullest. |
The company has been pursuing a workplace environment where worthwhile jobs are offered, and it is developing a personnel evaluation system, taking measures for the employee shareholding association, and establishing systems for incentives, income insurance, etc. so that employees can work with peace in mind. In this cumulative second quarter, the company raised basic pay and enriched a qualification allowance, etc.
![]() |
|
(Source: Company’s material)
The company will contribute to the earth environment by offering innovative demolition technologies.
① | To offer innovative demolition technologies for deteriorated social infrastructure. |
② | To provide reliable, safe demolition technologies for a low-carbon society and contribute to the earth environment. |
③ | To offer advanced demolition technologies as a professional wrecker by utilizing 3D technologies. |
The provision of innovative technologies is the company’s core business and strength. In addition to various patented methods, the company has adopted 3D technologies for dealing with large-scale projects.
![]() |
|
(Source: Company’s material)
The company will actualize an advanced recycling society, and contribute to the establishment of a sustainable society.
① | To offer technologies for appropriately disposing of harmful materials and pollutants and making them harmless. |
② | To develop a recycling business with high added value, with the aim of improving productivity significantly. |
③ | To coexist with local communities, and contribute to the development of regional environments in the future. |
Based on the alliance with REVER Holdings Corporation, the company hopes to get closer to these goals. The company has been performing environmentally friendly works, but will improve them further and offer one-stop services. Many of the company’s client companies operate business in the key industries, and the clients themselves are required to take environmental measures. The company plans to meet the clients’ requests.
![]() |
|
(Source: Company’s material)
Partnership for developing a sustainable (advanced recycling) society
① | The company aims to foster future-oriented partnership for achieving lofty goals beyond all barriers. |
② | The company aims to promote fair and equitable partnership among enterprises. |
③ | The company aims to attain goals by providing an advanced recycling society with new technologies, knowledge, and insight. |
Overcoming barriers, the company will concentrate on the fostering of partnership for achieving higher goals. In order to realize an advanced recycling society, the company will offer new technologies, knowledge, and insight with the aim of achieving goals. To do so, the company will cooperate with various companies.
4-3 Contribution to social sustainability and growth of profit through ESG management
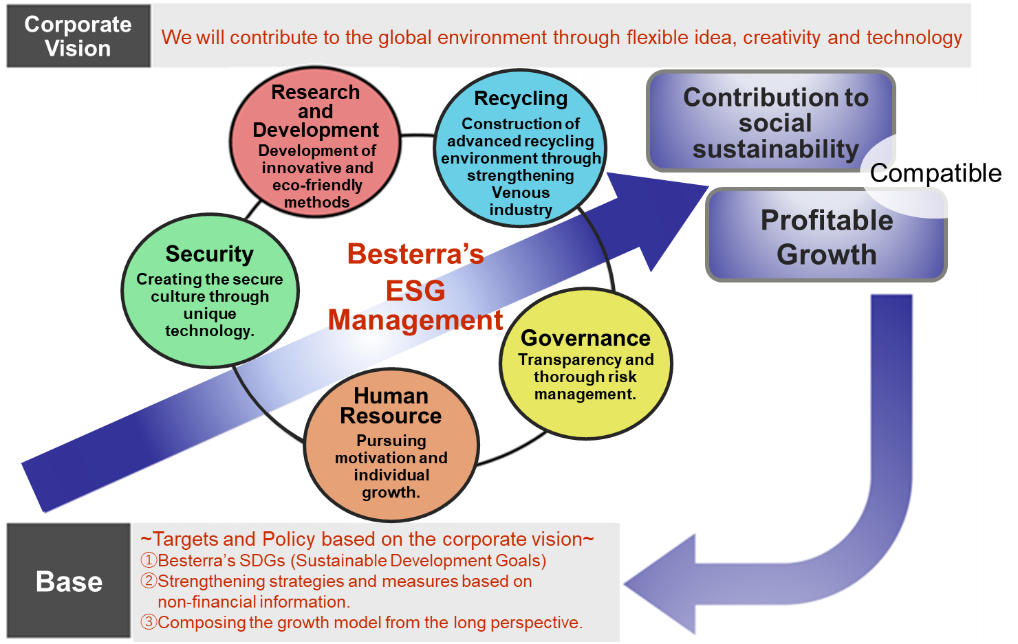
(Source: Company’s material)
The company gives top priority to “safety” as a dismantler. It will also work on R&D as a company boasting its technological capability. Furthermore, it will put energy into recycling, governance, and human resources. In detail, it will conduct ESG management by working on safety (creating a safe culture with its original technologies), R&D (developing innovative methods friendly to the earth), recycling (actualizing advanced environmental cycling by strengthening the venous industry), governance (thoroughgoing transparency and risk control), and human resources (pursuit of worthwhile jobs and growth of individuals), and contribute to social sustainability while growing profit. As the understanding of these activities is deepened, ESG investment will be made in the plant dismantlement and recycling industries.
5. Conclusions
REVER Holdings Corporation, with which the company signed a contract for capital and business tie-ups, is a top-class recycling enterprise in Japan, earns annual sales of 30 billion yen, and has 726 employees on a consolidated basis (as of the end of Dec. 2018). Their business would start with the disposal of industrial waste, including iron scrap from plant demolition, and the purchase of scrap, but in the mid/long term, they hope to develop an integrated system including demolition and recycling, and contribute to the earth environment. In addition, the footholds and networks of REVER Holdings Corporation around Japan will become strengths in the business of decommissioning and dismantling nuclear power plants, which will be operated on a full-scale basis (there are about 60 nuclear power plants in Japan, but decommissioning is expected to be determined for most of them in the near future). The structures inside a nuclear power plant are almost the same as those of thermal power stations except radiation-controlled areas. However, there are difficult promises with local residents about nuclear power plants, and there are many constraints on dismantlement. It is necessary to have meticulous meetings with local residents for discussing safety measures in advance and proceed with dismantlement as planned. Therefore, the company needs to listen to the voices of local people and enlist cooperation from local communities when proceeding with dismantlement, and entrust reliable enterprises and disposers. In this situation, the track records and networks of REVER Holdings Corporation would be helpful.
REVER Holdings Corporation disposes of many automobiles and home appliances, and recycles the shredder scrap produced by the disposal. Since shredder scrap includes a lot of waste plastics, they are apparently proceeding with a project for converting the waste plastics into solid fuel. According to “Measures for recycling waste from used automobiles” by the Ministry of Land, Infrastructure, Transport and Tourism, the recycling rate of used automobiles is about 75%, which is higher than those of other products, but the remaining 25% is disposed of as shredder scrap. It is said that there are problems, such as the illegal dumping because materials that are difficult to recycle are used. The business chances for both companies are expected to grow, as they make efforts to actualize an advanced recycling society.
<Reference: Regarding Corporate Governance>
◎ Organization type and the composition of directors and auditors
Organization type | Company with an audit and supervisory board |
Directors | 9 directors, including 2 outside ones |
Auditors | 3 auditors, including 3 outside ones |
◎ Corporate Governance Report Update date : April 26, 2019
Basic policy
In order to promote sound business administration and win social trust sufficiently, our company recognizes corporate governance as the most important issue, puts importance on the improvement of the soundness, transparency, and fairness of business administration, and complies with laws and regulations thoroughly, and all executives operate business while keeping in mind that “the violation of laws or regulations would lead to management responsibility.” In detail, our company disseminates and executes business pursuant to laws, regulations, and in-company rules thoroughly, by developing appropriate systems for making decisions about business administration, fulfilling duties, supervising work, conducting internal control, etc.
It is also important to reform management systems for “achieving appropriate share price” and “increasing share price sustainably” to emphasize shareholders and strengthen the function to check business administration, to establish global-level corporate governance. The results of such efforts would win the trust of society, increase corporate value, and satisfy shareholders.
<Reasons for Non-compliance with the Principles of the Corporate Governance Code (Excerpts)>
【Supplementary principle 4-1-3】
There is no concrete plan regarding the succession of the CEO (chief executive officer). As a policy for the selection of a successor in the Board of Directors meeting, we will select a suitable candidate by taking his/her character, insight and achievements into account. The Board of Directors will actively take part in activities of making and carrying out a succession plan.
【Supplementary principle 4-3-3】
Our company has not established a clear procedure ensuring objectivity, timeliness and transparency for dismissal of the president or CEO, but we strive to realize a mutual assessment by involving outside directors in the process of evaluation of nomination and remuneration of the Board of Directors, in order to carry out the assessment of effectiveness of the Board of Directors appropriately.
<Disclosure Based on the Principles of the Corporate Governance Code (Excerpts)>
【Principle 1-4 Strategically held shares】
From the viewpoint of business expansion based on business alliance, etc. with business partners, we will acquire and hold the shares of the business partners, etc. if we judge that this will contribute to the improvement in our mid/long-term corporate value. The board of directors constantly check whether the holding of the above-mentioned shares (strategically held shares) will contribute to the improvement in our corporate value, and confirm the purpose and rationality of said holding based on that check. Our company will exercise the voting rights of the strategically held shares appropriately, based on comprehensive judgment from the viewpoint of improving our corporate value.
【Principle 1-7 Transactions among related parties】
Our company conducts a survey on transactions among executives and major shareholders every year, to check whether there are any transactions among related parties. In addition, our company produces a manual for producing financial statements, and if our company makes any transactions with executives, the employee shareholding association, major shareholders, or the like, the internal audit division, the administrative division, the board of directors, and the board of auditors will deliberate about the necessity of said transactions to a sufficient degree, so that said transactions will not harm the common interests of our company and shareholders.
【Principle 5-1 Policy on constructive dialogue with shareholders】
Regarding requests from shareholders for dialogue (interviews), our company believes that we should express a positive attitude within a reasonable scope in order to contribute to sustainable growth and medium- and long-term improvement of the corporate value of our company. Aiming to promote constructive dialogue with shareholders, with the planning department designated as a department in charge of IR activities, our company holds financial results briefings targeted at financial institutions and investors semiannually and discloses corporate information as needed on our website and through the system of optional disclosure offered by Tokyo Stock Exchange.
This report is intended solely for information purposes, and is not intended as a solicitation for investment. The information and opinions contained within this report are made by our company based on data made publicly available, and the information within this report comes from sources that we judge to be reliable. However, we cannot wholly guarantee the accuracy or completeness of the data. This report is not a guarantee of the accuracy, completeness or validity of said information and opinions, nor do we bear any responsibility for the same. All rights pertaining to this report belong to Investment Bridge Co., Ltd., which may change the contents thereof at any time without prior notice. All investment decisions are the responsibility of the individual and should be made only after proper consideration. Copyright(C) 2019 Investment Bridge Co., Ltd. All Rights Reserved. |